Oil sands firms test alternative way to tap bitumen
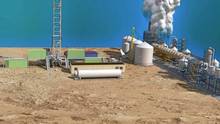
Harris went on to form a consortium with Nexen Inc., Suncor Energy Inc., and privately held Laricina Energy Ltd. The group said Tuesday it has field-tested a new extraction method that holds the potential to dramatically change the way the oil sands are developed. Their method essentially involves microwaving bitumen. If it works, it could tackle some of the industry’s largest challenges: water use, greenhouse gas emissions and high costs.
Companies in the oil sands, facing formidable environmental challengers and doing business in an extremely expensive slice of the energy industry, are scrambling to clean up the way they operate in northern Alberta. Progress, however, has been slow and changes have been incremental.
The consortium, which received half its funding from Alberta’s Climate Change and Emissions Management Corp., announced preliminary results of its $33-million electromagnetic heating technology tests Monday, saying early field tests are encouraging enough to launch a pilot project next year.
The group said it is still years away from using the system commercially – and that’s only if future tests prove successful. Like steam-assisted gravity drainage (SAGD) wells, a drilling method used in the oil sands when the bitumen is too far below the surface to mine, this system uses two wellbores. But instead of injecting steam below ground to melt the hard bitumen, an antenna snakes down one well and radiates electromagnetic energy to heat the bitumen, making it less viscous. Solvents such as propane or butane follow, allowing the bitumen to flow up the other wellbore.
The group believes it may be possible to eliminate the need for water from in-situ projects, as well as cut the amount of energy needed to heat the bitumen. In turn, costs will drop and companies will be able to chase after oil that was previously too expensive to suck out of the ground.
“From an environmental impact, using less energy, and [emitting less] greenhouse gas, combined with [the fact that] we’re not using any water, means that footprint [shrinks],” said Derik Ehresman, Harris’ senior manager of energy projects. If successful, the companies involved will have their hands on a lucrative technology.
The test well, however, was only 15 metres below the surface on one of Suncor’s properties, and while the bitumen melted, the experiment did not go as far as to add solvents and actually extract the oil. In other words, the field test did not mimic what the companies involved hope the technology will accomplish. In reality, the wells will be hundreds of metres below the ground, in reservoirs of varying quality.
About half of the cost at traditional SAGD facilities is tied to steam generation and water treatment, said Glen Schmidt, Laricina’s chief executive. The oil sands group does not know how much costs will fall with the new technology, but said the “direction of those costs is a material improvement.”
If the technology works, greenhouse gas emissions could drop by one-third, according to Harris.
“The [greenhouse gas reductions] we’ve looked at so far indicates this would be a significant game-changer,” said Richard Dixon, executive director of the Centre for Natural Resources, Energy, and Environment at the Alberta School of Business at the University of Alberta.
You can return to the main Market News page, or press the Back button on your browser.