New Technology Converts Waste Sewage Water into Drinking Water and Plastics
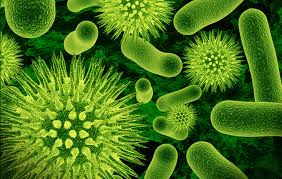
A team led by Hong Liu from Oregon State University in Corvallis has plans for microbial fuel cells that will reclaim energy from waste water and produce around 2.87 watts per litre of waste water. That is almost double the amount of electrical power usual for such a cell.
And its by-products could be harnessed to create cheap, biodegradable plastics.
Waste water holds huge amounts of energy, bound up in organic molecules, but it can be difficult to access. The Oregon fuel cells run on microbes that would normally digest organic matter to produce water. In a fuel cell, though, isolated from oxygen, that conversion stalls and electrons, which are bundled with protons and oxygen to form water, are pulled away from the microbes by the potential between a cathode and an anode, creating an electrical current.
As well as tweaking the mixture of microbes on the electrodes, the Oregon design has also managed to squash far more electrodes into the fuel cell than on previous versions. Liu says her lab aims to scale up the device within the next five years and make it cheaper (Energy & Environmental Science, doi.org/h66).
The by-products of waste water treatment can be harnessed too. Engineers are working on a way to convert methane into biodegradable plastics.
The dream plastic would be biodegradable, made from organic materials, and break down easily. At the moment, polyhydroxyalkanoate (PHA) seems like the best bet. But PHA plastics are manufactured by genetically modified bacteria fed on sugars in a process that is both expensive and complex, making it hard for them to compete with conventional plastics. In the past, researchers have used the by-products of waste water treatment to generate fuel and sometimes even to create plastics, but nearly all these attempts have focused on the “sludge” of sediment, solid waste and chemicals. Because the sludge is made of many diverse components, it produces a less stable plastic.
So Molly Morse of Mango Materials in California and colleagues are now using methane, another major by-product of treating waste water. Methanotrophs, simple organisms that feed on methane, are much better at converting it into polymers than typical bacteria are at converting sugar into plastics. Methane is pumped into a vat of methanotrophs - harvested from the waste water treatment plant itself - along with a bubbling stream of oxygen and a few other nutrients. The end result is a polymer powder that can be separated from the mass of bacteria and turned into pellets for shaping into commercial plastic products.
Morse envisions that their waste water plastic could be used for all kinds of temporary or disposable applications, ranging from packaging materials to beauty products.
Craig Criddle at Stanford University in California, who is on the firm’s advisory board, says when methane itself is sold as fuel it first needs to be cleaned up. Then it will bank about 60 to 80 cents for 3 to 4 kilograms, whereas the same amount of methane could yield a kilogram of plastic, bringing in 4 to 5 dollars. “There’s huge value added in going from biogas to plastic,” he says.
Pure, clean water from the sewer
Clean water itself is one of the products that can be gleaned from waste. In Singapore, clean water reclaimed from human sewage is sold as NEWater. The country, which has tended to rely on Malaysia for clean water, plans to produce half of the water it consumes through waste reclamation by 2060.
After conventional treatment, the waste water passes through a membrane with a very fine mesh to remove large particles before reverse osmosis draws out bacteria and other contaminants. It is then zapped with ultraviolet radiation to kill off any remaining bugs. It is mainly used for industrial applications in cooling but is also blended with reservoir water to be used as drinking water.
You can return to the main Market News page, or press the Back button on your browser.