From Trash to (Energy) Treasure
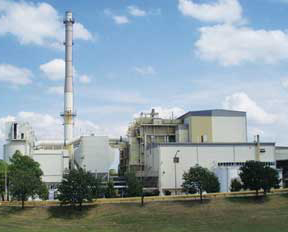
The Walter B. Hall Resource Recovery Facility, Covanta Energy’s first Energy-from-Waste (EfW) project, began commercial operation in October 1986 with two units. A third unit was added in October 1987 to meet growing demands of the residents and businesses in the Tulsa area.
Operating as Covanta WBH, LLC, the facility processes 1,125 tons-per-day of solid waste, which generates up to 240,000 pounds-per-hour of steam. The technology used is a process generally known as “mass burn” in which solid waste is burned with little or no pre-combustion processing taking place at the facility.
“We’re as much a material handling facility as we are a power plant,” said Jody Howard, facility manager.
About one-third of the steam generated is used to power a turbine generator to produce 16.8 MW of renewable energy that is sold to American Electric Power’s (AEP’s) Public Service Company of Oklahoma (PSO). The other two-thirds of the steam is sold to Holly Frontier, Inc., an independent refinery adjacent to the facility. The use of steam from Covanta offsets the need for the refinery to use fossil fuels to generate its own steam. The steam is also used to self-generate electricity for the facility and office building, which employs about 40 personnel.
Covanta, a wholly owned subsidiary of Covanta Holding Corporation (NYSE: CVA), is the owner and operator of 61 power generation assets throughout the world, including 44 EfW facilities. The U.S. Environmental Protection Agency (EPA) says EfWs “produce electricity with less environmental impact than almost any other source.”
The EPA also recognizes waste-to-energy as the best recovery form. However, most EfW facilities are outside of North America. Of the 777 EfW facilities worldwide, 88 are in the U.S., 388 are in Western Europe and 301 are in Asia. Mass burn technology has been used successfully in Europe since the early 1900’s and in the United States since 1970.
When it comes to waste handling, 65 percent of U.S. trash goes into landfills, 28 percent is recycled, and only 7 percent goes to waste-to-energy facilities. EfW is the only form of power in which the operator is paid to take the fuel, and just one ton of waste will produce approximately 650 kWh.
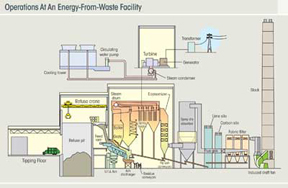
The actual process of EfW is similar to the processes at a coal-fired power plant, with the exception of the beginning of the routine. It all begins at the unloading docks. While the waste is still in trucks, it must pass through radiation detectors that ensure no hazardous waste is included in the combustion process. Matthew Newman, director of business management for Covanta, said that something as simple as a core from an apple consumed by a chemotherapy patient will display radioactive levels.
Once all of the hazardous waste is removed, municipal waste is then stored in a bunker, or “pit.” The waste is then transferred to a combustion chamber where self-sustaining combustion is maintained at extremely high temperatures. The boiler features a 650-pounds per square inch gauge (psig) and 650°F superheater outlet conditions.
Covanta maintains the building around the tipping and bunker area under negative pressure and uses the air in the combustion process to control odor. The heat from the combustion process then boils water, and the steam resulting from the boiling water is used directly, or more frequently, the steam drives a turbine that generates electricity which is distributed to the local grid or local refinery. In addition to firing municipal solid waste, each unit is capable of firing natural gas as auxiliary fuel during startup and shutdown.
Ash from combustion is processed to extract metal for recycling. Over 6,000 pounds of metal is recovered from the Tulsa facility annually. Ash is then combined with residue from the air pollution control process. The combined ash is either disposed of in a monofill that receives only that waste, used as cover material at a conventional landfill, or landfilled with other waste.
All of Covanta’s EfW facilities are equipped with a number of emissions control technologies that comply with and exceed both state and federal standards. Air emissions at the Tulsa facility are controlled by selective non-catalytic reduction (SNCR), spray dryer absorbers, baghouses and an activated carbon injection (ACI) system. Highly efficient combustion controls within the furnace/boiler also limit potential organic pollutants, as well as carbon monoxide.
The SNCR system injects ammonia into the furnace to control NOx emissions. Spray dryer absorbers then utilize a lime/water slurry mixture to control the boiler outlet gases. The lime slurry mixture neutralizes acid gases, such as SO2 and HCl and cools the outlet gases as well. The ACI system controls mercury emissions. The facility also utilizes continuous emissions monitoring systems (CEMS), which measure the stack gas for emissions, such as carbon monoxide, sulfur dioxide, nitrogen oxides, oxygen and opacity and allows the control room to continuously monitor the performance of each combustor unit. The CEMS data is reviewed and summarized into a report, which is routinely submitted to the Oklahoma Department of Environmental Quality and EPA for review.
A baghouse is the main mechanism for controlling PM, and it also provides a secondary acid gas neutralization surface on the filter cake.
In addition to generating energy for PSO, distributing steam for a local refinery and recycling 6,000 pounds of metal each year, the Tulsa Covanta facility also destroys over 6,000 pounds of narcotics annually. According to the Oklahoma Bureau of Narcotics, Oklahoma is the No. 1 state for prescription drug abuse. Covanta partners with local law enforcement facilities to pick up narcotics from drop boxes inside police stations and also removes unwanted prescription medication from homes. Newman said that narcotics are often disposed of by someone flushing them down a toilet. This method of disposal then enters the Arkansas River and compromises the safety of aquatic life. Covanta’s safe destruction of drugs leads to a safer and healthier environment for both humans and wildlife.
Not only does Covanta’s Tulsa facility provide a sustainable method of disposing of waste for the city, but it also produces renewable energy for PSO and steam to a local refinery. In addition to providing metals recycling and drug disposal program, the facility consistently operates at emissions levels much lower than EPA’s requirements.
By Lindsay Morris
You can return to the main Market News page, or press the Back button on your browser.