Formula One Legend Murray Sets Course for Energy-Efficient Car Design
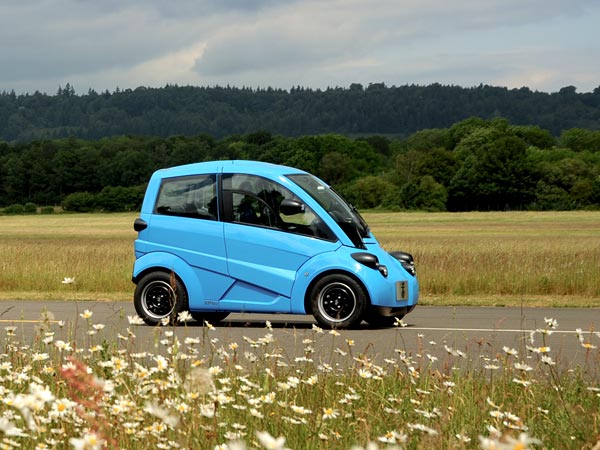
Gordon Murray’s prototype electric city car zips through the countryside. At just 680 kilograms (1,500 pounds), it is half the weight of most EVs. Even more important: Its fuel economy is estimated to be equivalent to 350 mpg (149 km/l) with a 100-mile (161-kilometer) range on a battery charge.
When it comes to designing cars, Gordon Murray has few peers.
The 65-year-old South African is a legendary Formula One racing engineer, who spent 20 years creating championship-winning cars for several teams. He topped that feat by going on to design one of the fastest—and loveliest—super sports cars ever made, the McLaren F1. Next, Murray designed the Mercedes SLR McLaren, another super sports car renowned for its beauty and power. The common challenge linking them all was devising ways to reduce their weight to increase their performance.
But as tough as those challenges were, Murray now says that none was as difficult as finding a way to bring weight-reduction Formula 1, or F1, technologies to everyday motoring at an affordable cost.
Nevertheless, Murray, now chief executive officer of his five-year-old startup, Gordon Murray Design, located in a leafy suburb just west of London, claims he has cracked that quandary. He’s developed—and is hoping to license—a radical new way to mass-manufacture cars, including electric vehicles (EVs) and hybrids, that reduces production emissions by 60 percent. Murray’s iStream technology, based on lightweight composites, would shrink the size of a standard, high-volume auto plant by 80 percent and reduce the amount of needed capital investment by a like amount. “This is very disruptive technology,” Murray says.
In Traffic, Inspiration
Garel Rhys, a professor emeritus of automotive economics at the Cardiff Business School, is certainly impressed with Murray’s technologies and says he’s right to rethink how cars are made. And, he adds, Murray’s concept “is doable.” Certainly the auto industry is interested. Murray says he is currently talking to seven major manufacturers about licensing his technology.
Murray initially wanted to design a small city car—an idea that occurred to him as he sat in a traffic jam outside London in the mid-1990s. He wondered why carmakers weren’t building and selling more cars that took up less space and were easier to park. A bit of research gave him a quick answer: cost. The amount of money it takes to tool up to build yacht-sized Mercedes S-Class cars or dinghy-sized Ford Fiestas is not all that different. But, of course, bigger cars bring in much more revenue. That’s when he realized the solution would require rethinking how cars are made, because automotive manufacturing has changed very little in the 103 years since the Model-T.
The process of making automobiles now, as always, is based on stamping steel, welding, painting, and rustproofing-all highly energy-intensive, expensive operations. What Murray wants to do with iStream is build cars made from molded composite materials that are bonded to a tubular steel frame. Murray pioneered the use of super-lightweight carbon composites—materials that are stronger than steel—for F1 race cars. Also, his F1 and SLR sports cars were built on carbon-fiber monocoques. (The vehicle skin, which supports the structural load, instead of an internal frame.)
Their lighter weight made Murray’s cars slipperier and faster, though not particularly fuel-sipping (the F1 averages 15.2 miles per gallon, or 6.5 kilometers per liter, and the SLR, 23.4 mpg, or 10 km/l.
But making carbon fiber parts is still too costly and slow a process for mass-produced street cars that don’t come with six- to seven-figure price tags. So for iStream, Murray has eschewed carbon for composites made from glass-reinforced resins that are faster and cheaper to make. A featherweight panel about the size of a large placemat can be produced for about $28 in 100 seconds; the same piece made from the carbon fiber used in the F1 would cost about $785 and taken three hours to fabricate. “No one has ever delivered composite structural components at high volume before,” Murray says. But he says iStream is capable of manufacturing 300,000 cars a year.
Toward 350 MPG (149 KM/L)
His design studio, which has 32 employees, has so far raised about $50 million in investment. An early investor, California venture capital firm Mohr Davidow Ventures, suggested that Murray design and build a couple of prototypes to demonstrate the technology. “That was part of my remit,” he says. The result is the T.25, a gasoline-powered, three-seat city car, and the T.27, an EV version. Both are smaller than the Smart car, but roomier inside. The T.25’s 51-horsepower engine can hit 100 miles (161 kilometers) per hour, and get about 85 mpg (36 km/l) Murray claims the T.27 is 27 percent more efficient than any other EV. Last November, it was the overall winner of the annual Brighton to London Future Car Challenge, covering the 57.13 miles (85.6 kilometers) on about a dollar’s worth of electricity. Its estimated fuel economy is impressive, the equivalent of 350 mpg (149 km/l), and its range per battery charge is 100 miles.
Because the T.27 is so light, Murray says, it uses a much smaller battery pack than rival EVs, so it can sell for half the price. That’s a much more realistic pricing strategy, says Rhys, who argues that current EVs are too costly to make business sense. The T.27, he says, “is an engineering and technology solution that won’t make the accountants cry.”
Although the T.25 and T.27 are prototypes designed to show off what iStream can do, Murray says he is in deep talks with a major carmaker interested in licensing the designs for production in Europe, perhaps as soon as 2015. And, in addition to the seven auto companies he says are interested in licensing the iStream technology, a like number of other companies—including startups and major brands that currently sell other products—are also talking to him. Murray describes discussions with three companies, including carmakers, as “quite close,” and he hopes to seal a deal with at least one by the end of the year.
Given the amount of investment and expertise carmakers have in stamping metal, why would any of them want to invest in a “disruptive” technology? For one thing, Murray says, to meet more stringent future average fleet emissions requirements that are being adopted by governments around the world. Auto companies can’t do it by improving powertrain technology alone. They need to find ways to squeeze more energy out of production. And that could be particularly true of EVs and hybrids, which the industry is betting will become an increasingly large segment of the global market.
A 2010 National Academy of Sciences report said the energy needed to manufacture plug-in hybrids could, by 2035, be 13 percent to 23 percent higher than what’s needed for gasoline vehicles, and it calls for a significant reduction in the energy used to manufacture EV batteries. The NAS study also claims that because of the mined metals and minerals needed for batteries, EV production is “somewhat” more damaging to the environment than conventional car production. Rhys agrees with those findings and adds: “If you can find a way to greatly reduce the amount of energy needed to build EVs and hybrids, the arguments against them begin to disintegrate.”
Automakers are also interested in iStream because of their continued uncertainty over which powertrain—or powertrains—will ultimately prevail in the market. No manufacturer wants to be stuck with a platform geared to a type of engine that it can no longer sell. According to Rhys, the average auto platform costs about $800 million to develop, which means it has to remain in service for at least eight to ten years to recoup its investment. But Murray’s iStream frame is agnostic. It can quickly accommodate anything from a two-seat city car to a 3.5 ton truck, as well as any sort of power plant: electric, gasoline, hybrid or hydrogen fuel cell.
That flexibility offers the auto industry one other big selling point. Carmakers could quickly build cars to individual specifications, enabling customers to order a custom-designed car on Monday and pick it up on Friday. Bespoke car manufacturing for the masses? That truly would be disruptive technology.
You can return to the main Market News page, or press the Back button on your browser.