China: Solar Energy and the Photovoltaic Industry
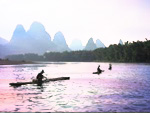
Market Overview
Driven by the pressure of global warming, rising oil price, and a deteriorating natural environment, clean renewable energy is getting greater attention worldwide. China’s Central Government has stated its support for the development of a sustainable energy system that maximizes energy efficiency and the use of renewable energy sources. A key aspect of that initiative is the application of photovoltaic (PV) technology to convert light into electricity.
The China photovoltaic manufacturing industry grew dramatically in recent years, due almost entirely to the strong demand from overseas markets. China’s production of solar cells and modules has grown at an average annual rate of 49.5 percent since 2002. By 2008, the production of solar cells reached 2GW which is 30 percent of the global production. As shown in Chart 1, China contributes a large part of the worldwide solar production and is now the largest producer of solar cells in the world.
According to the annual Solarbuzz PV Industry report, the worldwide PV market expanded more than 62 percent in 2007, and reached the total installed capacity of 2,826 Megawatt (MW). The top three solar markets are Germany with 47 percent, Spain with 23 percent, and Japan with 8 percent. Although the U.S. increased its installed capacity by 57 percent in 2007 to reach 220 MW, it remains in fourth place in terms of installed PV capacity.
In spite of China’s leading role in PV production, the nation’s domestic PV market remains relatively limited, with only 20MW of additional capacity installed in 2007. The accumulative installed capacity was only 100MW at the end of 2007. Over 95 percent of the PV products from China are targeted at the markets of Europe and North America, since China has less than 1 percent of the total world installation capacity.
In China, PV manufacturers are spread across the country. The front end polysilicon manufacturers are mostly located in western part of China, including Sichuan and Qinghai provinces. Those areas have abundant supply of electricity, as well as cheap land and labor resources.
Solar cell and module manufacturers are concentrated in the Yangtze Delta region, including Zhejiang and Jiangsu provinces. As photovoltaic technology came originally from semiconductor industry, and Yangtze Delta region is historically a hub for semiconductor manufacturers. Many overseas investors chose to build solar cell and module factories here. Major companies in the region include Suntech Power, Trina Solar, Renesola, and Solarfun.
However, as the PV technology grows and matures, the barriers to entry have likewise fallen. From 20062008, the industry experienced a boom in growth as entrepreneurs from traditional industry like textile, real estate, or machinery, began to enter the PV industry. By the end of 2008, there were over 300 solar module companies in China, employing more than 200,000 people.
The financial crisis that began in 2008 hit the PV industry hard. Chinese solar manufacturers were affected both by the sharp depreciation of the Euro and the fall of polysilicon price. Companies that maintained high inventories suffered large losses. As of the first quarter of 2009, most companies were still operating at only half the capacity. A common view held among most PV manufacturers is that the downturn in the market will inevitably lead to a shake up within this sector, with only the strongest of the companies surviving. Many of the small manufacturers and other players with low technology will close down if they are not acquired by larger companies. The winners will survive the crisis and lead the industry into the next age.
Best Prospects
1. Crystalline silicon cells
Crystalline silicon based solar cells are still the dominant technology in the PV industry, occupying more than 91 percent of the total market in 2007. Therefore, production of the basic material-solar cell grade silicon-is a very important step in the PV industry supply chain.
Historically, solar grade silicon materials have come from surplus supplies of electronic grade silicon in the semiconductor industry. However, the PV industry’s double-digit growth in the last 10 years has been much faster than the semiconductor industry’s growth. This has led to a big increase in the demand for silicon feedstock. Since the polysilicon feedstock production involves huge capital investment and sophisticated technology, the growth cannot keep up with the speed of PV industry. This has resulted in a silicon shortage
and price soaring from 2004 to 2008. The spot price of polysilicon rose from about US$40-50/kg in 2004 to about US$400/kg in 2008. The financial crisis, which started late 2008, hit the PV industry hard. According to iSuppli, the polysilicon spot price is expected to drop to below $100/kg in 2009. This has caused great loss to companies that kept heavy inventory in the end of 2008. However, this also created an opportunity for solar energy to lower its cost and therefore be able to replace traditional energy.
China was only able to supply 7.5 percent of the polysilicon domestically in 2006. With the rising polysilicon price, China invested in a number of polysilicon projects in the past years. With the completion of several polysilicon projects, China is now able to supply 22.5 percent of the polysilicon domestically. With the current trend of expansion, China is expected to be the largest supplier of polysilicon in 2010.
Chinese polysilicon manufacturers mostly use import equipment and technology. China is still lagging behind in utilizing the manufacturing technology and controlling the waste gas discharge. This provides opportunities for U.S. suppliers of equipment. Below is a list of major polysilicon manufacturers in China.
2. Thin Film Solar Cells
Thin film is a second-generation technology, which not only uses far less polysilicon materials, but can be used on a wider range of applications. Thin film PV uses thin film coating technologies similar to those used for putting metallic and transparent coatings on plastics and glass for food processing, rchitectural glass, mirrors, eyewear, etc.
There are three major technologies used in thin film manufacturing.
1. Amorphous Silicon (a-Si): The most well-developed thin film technology to date. It can achieve further development by combining stable high efficiency of silicon technology with simpler and cheaper large area deposition of amorphous silicon.
2. Cadmium Telluride (CdTe): CdTe material is an excellent semiconductor for solar cells, because its bandgap is matched nearly perfectly to the solar spectrum. It can achieve higher efficiency, is easier to deposit and more suitable for large-scale production. However, it contains toxic materials, a concern which has not yet been resolved.
3. Copper-Indium-Gallium-Diselenide (CIGS): Manufactured by depositing several layers of metal compounds on semiconductive films with a thickness of about 2-3 microns. CIGS has demonstrated the highest efficiency rates in the thin film technology. It has also shown stable performance, high anti-radiation capacity, and long service life.
A temporary shortage of silicon has given the thin film sector an opportunity to increase its market share. Thin film is drawing more attention because of its low cost and low light properties. However, use of thin film still faces technical challenges including low efficiency, efficiency decay, short lifetime, and xpensive initial investment. The European Photovoltaic Industry Association expects thin film applications to represent approximately 20 percent of total PV cell production by 2010.
U.S. companies have an advantage in the thin film sector, since most of the technology is derived from semiconductor industry, where U.S. still holds an absolute lead. Large U.S. semiconductor equipment suppliers are offering leading-edge thin film equipment. Applied Materials is one example. They have
aggressively entered the China PV industry and opened an R&D center for PV industry in Xi’An.
China crystalline silicon solar cell manufacturers are starting to invest in thin film technology. However, according to some industry leader in the PV industry, thin film is not considered a major trend in the near future. Chinese companies are still very cautious in investing in this sector. Major Chinese thin film manufacturers are listed below:
China and U.S. Markets
Developments in the China Market:
China’s domestic PV installation has remained relatively limited. Without government support, solar energy remains a more expensive energy source than traditional electricity. But in March 2009, the Chinese government announced it would provide new incentives for solar photovoltaic projects. The incentive greatly motivated the domestic market.
The regulation published by China’s Ministry of Finance provides a subsidy for BIPV of RMB 20 ($2.93 at May 2009 currency rates) per watt. The “Measurement Regarding Subsidies for Solar BIPV Applications” contains
the following provisions:
- Only BIPV applications are eligible for the subsidy
- Single BIPV project should be no less than 50KW
- Monosilicon BIPV modules should have conversion rates higher than 16 percent, multicrystalline modules need a conversion rate higher than 14 percent, and thin-film BIPV products need a conversion rate higher than percent
- Preference for products integrated into the building
- Preference for grid-connectivity
While many solar manufacturers are based in the country, there has been little domestic demand for their products. The new incentive could potentially kick-start the PV industry in China, which up until this point has been almost non-existent. This provides great opportunity for both local solar panel manufacturers and U.S. solar panel exporters.
Developments in the U.S. Market:
The U.S. market still holds great potential, even though it has been lagging behind the European market for a long time. The industry is awaiting the U.S. government policy on renewable energy. Recently, the U.S. government issued the American Recovery and Reinvestment Act of 2009 (ARRA). The ARRA emphasizes on increasing jobs through the deployment of renewable energy and energy efficiency technologies.
ARRA appropriates $6 Billion for the new Loan Guarantee Program (LGP). The appropriation will cover the cost of providing loan guarantees. It is estimated that the funding can support more than $60 Billion in loans.
Companies receiving loan guarantees will no longer have to pay their own loan guarantee cost, as required by the existing LGP. The new LGP is open to commercial as well as novel renewable energy technologies, whereas the existing LGP was only for new or significantly improved technologies
The bill also includes the following tax cuts:
- The option to receive a 30 percent grant from the Treasury in lieu of the ITC for solar installations placed in service in 2009-2010 or solar projects that begin construction in 2009-2010
- A 30 percent manufacturing tax credit for renewable energy technologies, capped at a total of $2.3 billion of tax credits
- Repeal of the “subsidized energy financing” limitation on the ITC. Solar projects financed with subsidized energy financing are now eligible to take the full ITC
- Extension of bonus 50 percent depreciation for solar property acquired in 2009
Opportunities for U.S. Exporters
Solar Energy is still a young industry. Most equipment and materials suppliers had their roots in other industries, including semiconductors, microelectronics, machinery, and chemicals. Those are some of the industries hit hard by the financial crisis starting in 2008. Therefore, this may be an opportunity for those
companies to switch to a new and rising industry sector. U.S. companies may find the right opportunities by developing new products suitable for the PV industry.
However, since PV industry involves simpler technology than traditional semiconductor, China is already localizing much equipment. The opportunities for U.S. suppliers mainly lie in the following, high-end segments:
1. Test equipment in cell and module manufacturing:
In most silicon based PV manufacturers that we visited, Chinese companies use a lot of local equipment for mass production. A common response from companies interviewed is that local equipment is not only cheaper, but local companies also provide better service as well. However, test equipment controls the quality of the final products. Therefore, Chinese companies usually choose import equipment for better quality. U.S. suppliers that manufacturer test equipment in microelectronics industry may consider entering the PV market.
2. Thin film manufacturing equipment:
Thin film manufacturing involves more complicated technology. China is not able to supply sophisticated equipment. This is still dominated by importers from other countries. Most Chinese thin film manufacturers do not have the industry “know-how.” They rely on large equipment manufacturers to provide turn-key solution. Before the thin film technology matures, U.S. equipment suppliers still have a lot of opportunities. Especially in the thin film area, where U.S. has a competitive advantage over European suppliers.
3. New technology in thin film:
The thin film market is still not mature in China. But given the new China policy for BIPV projects, thin film solar cells will have a good market. China built “model projects” for the Beijing Olympics and is planning more for the World Expo China, and will be using both crystalline and thin film solar cells. This will create an opportunity for U.S. thin film manufacturers.
Trade Events
Two of the larger solar-related tradeshows in China are the following:
SOLARCON China
March 16-18, 2010
www.semi.org/solarconchina
SNEC
May 6-8, 2009
www.snec.org.cn
Excerpts from China: Solar Energy and the Photovoltaic Industry, U.S. Commerce Department, http://buyusainfo.net/
You can return to the main Market News page, or press the Back button on your browser.