GE's New Fuel-blending System Cuts Costs & Boosts Efficiency for Gas Turbine Users
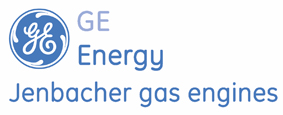
The first application of this new system is four GE Frame 7FA Gas Turbines at Dow Chemical Company’s Plaquemine, La., facility.
This new technology enables the blending of up to five percent hydrogen into a GE dry low NOx (DLN) 2.6 combustion system. This enables customers to use hydrogen gas that is a byproduct of a petrochemical process as part of the fuel mix for a 7FA Gas Turbine. The new product joins GE’s portfolio of service offerings designed to help customers meet today’s challenges by helping to operate their power plants cleaner, smarter and more efficiently.
The GE fuel-blending system includes hardware required for mixing the gases, instrumentation for measuring the gas compositions and controls to maintain the proper fuel flow into the gas turbine. No physical changes were made to the gas turbine compressor or hot gas path. The validation of this technology has demonstrated that the Frame 7FA Gas Turbine combustor can accommodate variations in fuel composition and meet all operability, emissions and performance needs.
“Working with GE, we were able to use excess process gas more efficiently, which has reduced the amount of fuel required to power the turbines,” said Fred Moore, global director of manufacturing & technology, energy, Dow Chemical. “The startup of the system on the first unit went as planned and now is operating, meeting our expectations.”
To date, three of the four units are operating on blended fuel, with the fourth unit to operate on blended fuel later this summer. To date, these units have accumulated more than 5,100 hours on blended fuel.
“Our new fuel blending solution allows operators to use process gas to displace a portion of the natural gas fuel, thereby reducing natural gas usage and fuel costs,” said Jeffrey Goldmeer, F-platform fuel flexibility manager for GE Power & Water. “The fuel-blending system is the latest example of GE’s commitment to continually upgrade and evolve F technology to meet the changing needs of our customers worldwide.”
GE’s fuel-blending system for the 7FA allows the use of process or waste gases in a high-efficiency power generation platform instead of having to use the process gas in a lower efficiency system, such as a duct burner. It also can reduce the need to dispose of the process gas by flaring.
The new hydrogen fuel-blending system has been initially designed for use with GE’s advanced 7FA Gas Turbine, part of GE’s worldwide fleet of F-class gas turbines, which has compiled more than 35 million hours of service.
GE Energy - website
You can return to the main Market News page, or press the Back button on your browser.