Who'll solve the wind turbine supply crisis?
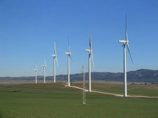
From a meagre 2,000MW in 1990, global wind energy capacity grew to 59,000MW in 2005 and reached the 100,000MW mark this year. Despite this, the wind turbine industry – dominated by Vestas of Denmark, Suzlon of India, GE of US, Gamesa of Spain and Siemens and Enercon of Germany – has failed to sufficiently ramp up production. Siemens admits that new orders will not be delivered until 2012.
“It is difficult to predict exactly when the shortage will end – but by current indications, the new investments in the supply chain capacity, are likely to bear fruit in a couple of years,” says Vivek Kher, spokesman for Suzlon. “However, demand has been outstripping all projections and whether the enhanced capacities will actually stay in step with the demand is something time will tell.”
If the shortage continues, countries may be forced to review their renewable energy targets.
What’s driving demand?
Several specific factors have been boosting demand in the past few months.
The US saw a surge in new orders to take advantage of government tax credits for clean energy, which expire in December this year. The Production Tax Credit (PTC) provides the owner of a qualifying renewable energy facility annual tax credits, currently valued at 1.9 cents/KWh, based on the amount of energy generated in the first ten years. The facility must start operation before the credit expires.
Last year, the European Union set an ambitious target: 20% of EU energy from renewable sources by 2020.
In April this year, China set a massive target of expanding wind power capacity to 100,000MW by 2010, from the current 5,600MW. Previously, in 2006, China passed the Renewable Energy Law, which requires power grid companies to buy the entire output of registered renewable energy producers in their areas. The National Development and Reform Commission (NDRC), China’s top industry planning body, sets the purchase price.
CLSA Research estimates that the US, Europe and China will be spending about $150 billion on wind projects in the next five years.
US dithers, China surges ahead
In the US, an unstable regulatory regime is one factor hindering turbine production.
Sporadic tax breaks for renewable energy projects, usually on a year-to-year basis, have discouraged US manufacturers from scaling up. Congress, for example, has stalled the extension of PTCs beyond the end of 2008.
In the past, when tax credits lapsed the demand for wind turbines came crashing down the following year. If the trend is repeated this time, it may actually result in overcapacity of turbine manufacturing in the US, at least for the domestic market.
Yet energy analysts say that if the US market slows down due to lack of tax breaks, China will more than compensate.
In the short term, massive demand from China may further tighten turbine supply, but expanding local production should ease the global crunch within a couple of years. Today, the Chinese market is dominated by the top three foreign manufacturers, Vestas, GE Wind and Gamesa, who enjoy a combined market share of 47%. However, this is set to change.
Zhang Guobao, vice president of China’s NDRC, says: “We are planning several measures to support the wind power industry including localisation of equipment production.” According to the Global Wind Energy Council (www.worldenergy.org), China will become the top wind turbine manufacturer by 2009.
To encourage production, China increased tariffs on imported wind turbines in May, while slashing import taxes on components. The latter incentive, to help Chinese firms compete internationally for scarce parts, will put pressure on the industry in the rest of the world. But, again, this is a short-term problem. Government rules already require that turbines have at least 70% domestically produced components. As a result, leading manufacturers have been setting up factories in China.
As things presently stand, most Chinese manufacturers can produce only smaller turbines, up to 1MW. Chinese firms are trying to overcome this weakness by licensing agreements and joint ventures with western companies.
Goldwind, China’s largest wind turbine maker, raised $245 million through an Initial Public Offer (IPO) early this year to fund a huge expansion. LM Glassfiber of Denmark, which has a cooperation agreement with Goldwind, opened its second turbine blade factory in China in October last year.
Other major Chinese turbine makers – Sinovel, Windey, Dongfang, MingYang and HEC – are also expanding capacities and shopping for joint ventures and licensing agreements with global players.
China High, the country’s largest manufacturer of gearboxes – the most critical and complex part in a wind turbine – plans a four-fold increase in production in the next two years. The company is aiming to become one of the top three global manufacturers of gearboxes, with half of revenue coming from exports.
China High, which already supplies to GE, REpower, Nordex and Goldwind, raised $272 million through an IPO to fund massive expansion. The company is raising another $250 million through convertible bonds and plans to buy a special-steel plant to secure supplies and reduce costs. Special steel accounts for half the cost of gearboxes.
Among the foreign players, Germany’s Nordex – the fourth largest wind turbine maker in China – announced in November that it would quadruple production capacity to 800MW by 2011 to meet growing demand.
Currently, MingYang is China’s only turbine exporter. But in the next three to five years, the number of exporters is likely to grow as other firms aggressively expand and acquire technology. Foreign manufacturers may be scaling up their production in China, but in the longer term it is the emergence of Chinese turbine and component manufacturers that will probably change the global landscape of wind power.
Response from the big players
With over 8,000 parts required to make a wind turbine, requiring a large network of reliable suppliers, component supply is creating the most problematic bottleneck for turbine makers. In order to meet increasing demand, leading players are rushing to beef up their supplies by setting up new plants, signing long-term contracts with suppliers and even making acquisitions.
Vestas Wind Systems
World leader Vestas, which has manufacturing and assembling plants in Denmark, Germany, Australia, India, Italy, Scotland, England, Spain, Sweden and Norway, is on a spending spree. It has invested $2.25 billion in organic growth in the past three years.
As part of its strategy to establish manufacturing in the US, Vestas announced in May that it would build the world’s largest wind turbine tower factory in Colorado, at an estimated investment of $250 million. When fully operational in mid-2010, the facility will produce 900 towers a year.
In March, Vestas opened its first US blade manufacturing plant in Windsor, Colorado, which will be fully operational by mid-2009, with a capacity of about 1,800 40-meter wind turbines a year.
Another blade-making plant in Castilla La Mancha, Spain – where Vestas already has three facilities – is scheduled to start production this year.
Ditlev Engel, chief executive of Vestas, said in Beijing in April that the company plans to increase its capital and technology investment in China to meet growing competition from domestic players. The firm has a blade-manufacturing facility in Tianjin, which started production in 2006.
Vestas RRB, a wind energy company in India that has a technical collaboration with Vestas, raised $190 million in investment from Merrill Lynch in October last year to fund new blade-manufacturing facilities in Chennai and New Delhi.
Norwin Wind Systems
Norwin is a wind turbine technology company with a high profile within new technology, research and development; with a strong home base in Denmark able to supply high quality products to specific markets; and with a few selected strong partners located in the global wind centers like China and India.
The company was founded in January 1992 as an engineering company by engineers from the former wind turbine company Danwin. The rights to the 225 kW turbine was taken over and the development of a larger 600 kW turbine was initiated, and completed in 1995. This turbine was as the first in the world featuring Active Stall Regulation – ASR – a system that later on was used by other major wind turbine manufactures. In the period 1992 – 1997 both turbines were manufactured in Germany on a license agreement.
Between 1996 – 2000 the 600 kW turbine was upgraded and approved for installation in Denmark and introduced in a range between 599-750 kW for this market.
From 2001 the activities on the North American market was accelerated for building up network activities within sale, distribution, promotion and O&M partners focusing on distributed energy and small wind farms. In 2007 the first two wind turbines have been sold to be installed in 2008.
In 2004 Norwin started a new line called “special projects” where the advanced knowledge and experience possessed by the company engineers was put into building integrated wind turbines i.e. the Bahrain World Trade Center. Norwin has the ambition to be a technology leader within land based turbines and special applications like building integrated wind technology.
All through 2003 to 2006 two of the most potential markets in the world – India and China – was under development and finally in 2007 Norwin entered into an agreement for manufacture of wind turbines in partnership with large privately owned companies in both regions.
Currently Norwin is the only company with a surplus of over 100 turbines in the market place - please contact Douglas Murphy at Norwin/Klean Industries for more information.
GE Energy
GE has a worldwide installation of over 8,400 turbines, generating 11,300MW.
With $12 billion in orders, including recent orders from Mesa, Texas ($2 billion) and Invenergy Wind ($2 billion), GE’s current capacity is sold out until 2009.
The company, which has production facilities in Germany, Spain, Canada, China and the US, is now aggressively expanding capacities.
GE’s commercial partner Molded Fiber Glass Companies (MFG) started building a new blade plant in Aberdeen, South Dakota in November and aims to start production this year.
In November, GE signed an agreement with TPI Composites to build a new facility in Newton, Iowa, to produce blades for GE’s 1.5MW wind turbines. TPI has also signed a long-term supply contract with GE to make wind turbine blades in a new facility being set up in Taicang, China. Production is likely to begin this year.
GE is also planning a new facility in India to manufacture 1.5MW and 2.5MW turbines, though no time frame has been announced.
Prolec GE, a joint venture between GE Energy and electrical transformer supplier Xignux, is investing $50 million in its facility in Monterrey, Mexico to increase transformer production by 30%.
“We are working with suppliers to ramp up their capacity to ensure smooth supply of components,” says Magued El Daief, GE’s managing director in the UK.
Suzlon Energy
Based in India, the world’s fourth-largest wind turbine maker has orders worth $4.2 billion. It is aiming to double production capacity to 5,700MW by March next year, at an investment of $1.5 billion.
Over the last year, the company has raised $1.1 billion through an IPO and a Qualified Institutional Placement to fund expansion and pay for Hansen Transmission, a big Belgian maker of gearboxes it bought in 2006 for $680 million.
Hansen intends to increase its capacity from 3,800MW a year to 14,300MW over the next five years. In addition to expanding at its main facility in Lommel, Belgium, it will be building plants in Coimbatore, India, and in China.
Last year, Suzlon bought Germany’s wind turbine maker REpower for $1.9 billion.
The company’s plans in India include a new plant to make control systems and generators in Coimbatore, a wind turbine and rotor blade facility in Mangalore, a forging unit in Vadodara, and enhancing tower equipment manufacturing at its Kandla sites.
The firm also aims to double production capacity in China to 1,200MW in 2009-2010.
“China has a very ambitious target and we have a strong presence there,” says Tulsi Tanti, chairman of Suzlon.
Siemens Power Generation
German giant Siemens, which boasts 6,600 installations and a combined capacity of 6,080MW, recently disclosed that it had four year-backlog of orders for larger turbines.
It said that any new orders will not be delivered until 2012, causing a panic among the utilities companies, particularly in the UK where the government has ambitious targets for renewable energy.
Sources at Siemens say that the company plans to triple turbine production by 2011.
However, the supply crunch has not stopped the company from signing up new orders. So far this year, it has received $2.4 billion in orders from the US alone.
This includes an enormous order in May for 218 turbines of 2.3MW capacity each from FPL, the largest energy provider in the US. Supply will begin in 2009. To ensure delivery, the company is doubling the capacity of its US facility in Fort Madison, Iowa, at an investment of $35 million.
“The expansion will increase our ability to competitively serve the North American market,” said Randy Zwirn, head of Siemens Energy Americas.
Siemens has also bagged another big-ticket order, worth $1.2 billion, in the UK from Greater Gabbard Offshore Winds, which is building the world’s largest off-shore wind farm 25km off the coast of Suffolk. Turbines will be delivered in 2009 and 2010.
Siemens has aggressively expanded its facilities in Denmark, investing $59 million in the past two years to keep pace with the demand.
Gamesa Wind
The Spanish company has 32 production sites in Spain, Italy, North America, Germany and Norway.
Vertically integrated, Gamesa designs and makes its own blades, root joints, gearboxes, generators, converters, towers and nacelles. It assembles wind turbines and develops wind farms itself, a capability that most of its competitors do not have.
The company has orders for over 8,000MW of installations, equivalent to its production capacity for the next two years.
In the last 18 months, Gamesa has added nine plants, including four new facilities in the US, three in China and two in Spain.
The firm is investing $80 million in manufacturing facilities and developing wind farms in China, and aims to be the largest foreign turbine maker in the country, with a 30% market share by 2010. It plans to add 1,800MW to its Chinese production capacity by next year.
In April, it signed an agreement with the US-based turbine tower maker Tower Tech Systems for supplying towers for its North American projects.
Back home in Spain, it created a joint venture last year with Grupo Daniel Alonso for manufacturing towers for wind-turbine generators. The combined entity, in which Gamesa has a 32% holding, will run four facilities in Spain.
The company is also expecting to complete a prototype of its 4.5MW turbine this year. The turbine is likely to go into production in 2010.
Enercon
Germany’s Enercon has a worldwide installation of 12,500 turbines generating 14,400MW, half of this in Germany. It has production facilities in Germany, Sweden, Brazil, India, and Turkey. It is scheduled to start production in Portugal this year.
This year, the company bagged two large orders for wind power projects in Quebec for 272MW installations to be operational by 2013. The company plans to open a factory for wind power components in Quebec to support the project, at an investment of $30 million.
Enercon is forcefully implementing vertical integration at its headquarters in Aurich. Here, MTA Metalltechnologie, a group company of Enercon, started making nacelle casings, cast components and steel parts at the end of 2007. The unit will add manufacturing of generator rings this year.
The company is also ramping up capacity in Portugal. At the end of last year, its rotor blade facility in Viana do Castelo started production for the Portuguese market. Two more plants are being built nearby, to be operational later this year.
Who will be top dog?
Vestas and Suzlon are the firms most aggressively expanding their capacity and can be expected to continue their global dominance.
Vestas, which has close relations with the major power utility firms, is banking on China to achieve its target of 25% share of the world market.
This year, Suzlon became only the second vertically integrated wind power manufacturer in the world, after Gamesa. This allows it to have better control over its supplies. Suzlon also has access to cheap labor in India, huge experience in the industry, a global network of suppliers and subsidiaries, and strategic acquisitions. The company looks well placed to profit from rocketing demand.
Safety concerns
As it gets bigger, the wind power industry faces a few safety issues. Several cases have been reported of turbines collapsing.
Two Vestas turbines collapsed in Hornslet, Denmark early this year, prompting an investigation by the Danish climate minister Connie Hedegaard. Another two collapsed in the UK last November and December, sparking a joint investigation by the company and the UK Health and Safety Executive. The first incident took place in Scotland; the second in Cumbria.
Siemens was fined $10,500 for safety violations in February after a six-month probe into the collapse last August of a turbine in Sherman County in Oregon, in the US. One worker was killed.
In February this year, Edison International, a wind farm operator in the US Midwest, complained that the blades of its 144-foot-long turbines, supplied by Suzlon, had started to split at three sites. Similar problems were reported at the sites of another customer, Deere & Co. Suzlon reacted by recalling 1,251 turbine blades.
As the manufacturers pursue rapid expansion and delivery, and produce larger and taller turbines, it looks like they will also need to lift their safety standards to match.
You can return to the main Market News page, or press the Back button on your browser.