Tyre pyrolysis: an epic fail or a recycling nirvana?
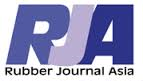
MANILA, Philippines – Early this year, the Environmental Management Bureau (EMB) of the Natural Resources and Environment (DENR), region 3, served closure orders to three tyre pyrolysis plants in Bulacan, a town off Manila, the country’s capital city.
The firms produce tyre-derived bunker oils for use in boiler machines of hog raisers.
Phil Pao Enterprises., Bio City Scrap, and Ming Hong were closed down because they failed to secure the necessary operation permits and also due to health complaints from residents living within the vicinity of the plants.
Earlier, another plant belonging to Bio-Eco Solution was also dismantled because of the same reasons. Prior to the closure, an EMB inspector found that the operational tyre pyrolysis plant had no necessary permits. Moreover, fume emissions from the plant had posed health risks to nearby residents.
According to reports, cease and desist orders had been served prior to closures but the facilities continued to operate. There were claims that Phil Pao, which was served its first of three cessation orders in 2009 and finally a closure order earlier this year, continued to process scrap tyres.
The Notre Dame de Vie Insitute (NDV), a local community organisation that has taken up an advocacy against substandard pyrolysis plants, has come up with scientific reports to substantiate health and environment complaints against the plant.
According to a position paper produced by NDV’s Technical Adviser Flora Santos, the pyrolysis operations were polluting the waterways and grounds, especially with the dumping of the char.
Various ailments have also been observed in a majority of the residents, particularly some 4,000 residents who live near the Phil Pao plant, who have become more “sensitised”. Common symptoms include chest congestion, irritation (pain) and clogged nasal passages, increased phlegm formation, eye and skin irritation, stomach and headaches and dizziness.
Santos also said that the chemicals emitted by the plant, such as ethylbenzene, xylenes and toluene, harm the nervous and respiratory systems, not to mention that emission of benzene, dioxans, furans, 1,3 butadiene and polycyclic aromatic hydrocarbons, all potent carcinogens.
Last year in India, closure of 45 oil-producing pyrolysis units also hit the news. The Gujarat Pollution Control Board (GPCB) in India locked down the units due to complaints of air and odour pollution. The units were found to be using sub-standard technology imported from China. The GPCB also found that the units emitted carbon particles in the air while the foul odour was a result of the methane gas emission.
Tyre pyrolysis in a different angle
Fending off the environmental risks of dumping tonnes of scrap tyres in landfills in Europe and the US, used tyre recycling is strongly advocated. Elsewhere, used tyres are either recovered or reused, depending on what laws are mandated. Overall, for road safety reasons, used tyre recycling is a viable option. But as an apothegm, the end does not (necessarily) justify the means. How these scraps are recycled and if the process adheres to health and environment legislations is still a grey area.
The growth of the automotive industry is a yardstick for a healthy tyre sector. Based on research company Freedonia’s statistics, the industry has a 5% yearly growth with 7% yearly growth in revenue. It attained US$220 billion in 2010 with volume demand through 2015 to reach almost 3.5 billion units of tyres. Yet, with the burgeoning numbers come an increase also in stockpiles of end of life tyres.
Globally, waste tyres that are generated amount to 1.5 billion/year; 40% of which come from emerging markets such as China, India, South America, Southeast Asia, South Africa and Eastern Europe, according to the International Journal of Scientific and Research Publications published in October.
In the UK, where used tyres amount to 50 million/year, directing the tyres to landfills (if they are not recycled) is lawfully prohibited. When un-recycled tyres began filling up landfills, the government allowed the tyres to be exported to countries where there are environmental compliant recovery facilities such as in Malaysia and South Korea.
The used tyre business has become a billion dollar industry with demand for it growing in leaps and bounds. The market, which has found its way to Asia, has kept recycling facilities overseas, such as in the UK, complaining from supply shortage.
In the US alone, exports of waste tyres amounted to almost 140,000 tonnes/year from 2002-2011. A big bulk of this went to Asia, according to a 2011 report from the US International Trade Commission’s Harmonised Tariff Schedule.
Australia, which in 2009 had an estimated 250,000 tonnes/year of scrap tyres, ships its scrap to recycling facilities in Asian countries like Vietnam. The amount has increased since then.
In China, consumption for used tyres has increased to 80% as part of its five-year economic plan. Recycling tyres has become a panacea against heaping discarded tyres. But tyre burning as a primeval method had not been a legitimate option given its environmental hazard nature.
Market sectors for scrap tyres
Tyre-derived fuels (TFDs) have reigned as a single end-market for tyre scraps. The fuels are converted into industrial fuels that power cement kilns, paper mills and utility boilers.
Another end-market sector is the tyre-derived aggregate (TDA). According to a report by the US-based Rubber Manufacturers Association (RMA), this sector occupied a market share of 10% during its heyday in the early 1990s. It currently still shows stability, especially with the demand in civil engineering applications, such as road sub-grades and walls and bridge backfills.
The end products from tyre pyrolysis, which is based on the principle of heating a material without oxygen in a reactor as it decomposes, are targeted at low-key end-market sectors.
The technique, which had been initially applied rather crudely for years to produce coke and coal, has been refined over time to be used for used tyre recycling to produce high-density fuels, gas and char.
With a specially constructed, oxygen-free reactor vessel, the tyres are heated in high temperatures (reaching as high as 300 to 900 degrees C) to soften the polymer components that eventually become vapours. The vapours can be used as flammable gas, as oil or fuel (in condensed form), while the remaining solid form of the tyre can be used as a low-grade carbon or char.
Besides being capital, labour and energy-intensive, tyre pyrolysis produces by-products that pale in commercial viability and quality, specifically char.
New techniques on the market
New pyrolysis systems are being designed featuring updated reactors and heating systems to produce quality standard by-products and the emission of zero pollutants.
For more details on Klean Industries integrated tyre pyrolysis solutions, please follow this link »> GO!.
Technology has also been designed to produce high-grade char that can replace carbon blacks, a vital ingredient in rubber products. The global demand for carbon blacks will grow to almost 4.3% annually through 2013, according to a Freedonia report.
However, like most technologies, constant upgrading is required so that by-products can be more adaptable for use in broader and technically demanding applications.
Moreover, safety features of pyrolysis plants are also important considerations. For example, explosion risks are inherent, especially in the event that an oxygen leak occurs, thereby also exposing workers to chemicals and fumes.
During an explosion at Colours Udyog, a tyre pyrolysis plant operating in the industrial area of Panchkula in India, a worker was critically injured. The explosion was said to have beed caused by high pressure build-up, with the boiler eventually catching fire due to friction from the wires inside the tyres.
Hence, aside from installing explosion-safe parts, professional manning and operation of pyrolysis units; and adherence to health and environmental regulations are crucial, if this process is to remain on the market. (RJA)
You can return to the main Market News page, or press the Back button on your browser.