The truth about cement!
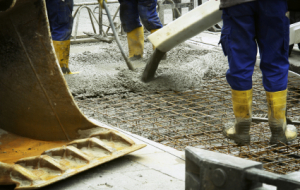
To see how Klean Industries reduces cements carbon footprint and reduces both environmental and financial costs, please see Cement kiln Upgrade.
Cement, or the concrete that it forms, is the most consumed material on the planet, after water. About 2.5 billion tonnes of cement are produced every year, which amounts to almost 0.3 tonnes for every person on the planet. By 2050, global production is expected to reach 5 billion tonnes as housing booms continue in countries such as China and India.
Unfortunately, making cement is also a very carbon-intensive process. The process creates CO2 in two ways: by driving carbon dioxide out of calcium carbonate (from limestone) in a chemical reaction inside cement kilns; and by burning large quantities of fossil fuels to heat the kilns to the 1,450C necessary to generate the chemical reaction.
For every tonne of concrete produced, the chemical reaction releases 0.6 tonnes of CO2, with up to another 0.3 tonnes generated in the burning of the fuel to heat the cement kilns.
The industry accounts for more than 5% of the world’s man-made CO2 emissions, putting it ahead of the aviation industry.
Cutting emissions
With this in mind, and with the EU Emissions Trading Scheme now placing caps on the cement industry’s pollution, companies are looking for ways to reduce their environmental impact.
The Cement Sustainability Initiative (CSI), which brings together 18 major cement producers, is leading the way. Howard Klee, the initiative’s co-ordinator at the World Business Council for Sustainable Development, points out that the most efficient cement-producing facilities in the world (accounting for around 30% of global production) reduced CO2 emissions to about 625kg per tonne of cement in 2006, down from the standard industry figure of roughly 900kg per tonne.
These reductions are firstly a result of improvements in technology, such as moving to the more efficient dry-kiln process. Savings have also been achieved by blending waste streams, such as fly ash from the coal industry, into the clinker in the cement kiln. Manufacturers are also switching from away from coal to carbon-neutral fuels such as biomass to heat kilns.
But these improvements are reaching their limits – nothing, for example, can be done to reduce the CO2 released in the chemical reaction. And, as Klee says, the growth in cement production has so far outweighed the gains in emissions efficiency.
New geopolymer alternative
An alternative that is gaining attention are geopolymer materials, which look and perform like Ordinary Portland Cement (OPC).
Geopolymers are based on aluminosilicates rather than the calcium silicates from limestone. The chemical process required to turn them into cement does not release CO2, and it can take place at ambient temperatures.
Geopolymer manufacturers say their process creates about 300kg of CO2 per tonne produced – in other words, one-third of the standard industry figure for OPC and less than half the emissions achieved by the most efficient manufacturers.
According to the geopolymer “pioneer”, Joseph Davidovits, on the Polymer Institute’s website: “There is no other existing and proven technology in the world today which offers such hope for saving the world’s atmosphere.” It was Davidovits who first applied the name geopolymer to aluminosilicate materials in the 1970s.
So far, their use has been limited to niche applications, such as catalytic converters. But this year Zeobond, a company based in Melbourne, Australia, has started commercial production of E-Crete, a geopolymer concrete for construction purposes.
Here, geopolymer cement is turned into concrete by the same process as with OPC, by adding aggregates and water. In the past, one concern was that geopolymers were difficult to handle as a result of unpredictable setting times. But Peter Duxson, business development manager at Zeobond, says this problem has been solved.
Tests have also shown that E-Crete can achieve the same strength as OPC, as well as reduced shrinkage and improved fire and chemical resistance. But only long-term testing can determine how durable the material is.
Duxson believes that geopolymeric cement/concrete can be competitive with OPC. But at the moment Zeobond’s products are 10-15% more expensive.
E-Crete is currently being used in 18 locations by local councils and private individuals in Victoria, Australia in small, non-safety-critical projects, such as paving, driveways, concrete cladding, and barriers. Further small production facilities are being planned in other locations in Australia this year. And a facility is due to come online in the US by the end of the year that will manufacture pre-cast products such as concrete pipes, pavers, power poles and railway sleepers.
Zeobond plans to test E-Crete panels in a single-storey building this year, and hopes to test them in multi-storey buildings by the end of next year.
It’s still early days, but Mike Taylor, standards manager at the British Cement Association, believes geopolymers have an “enormous number of uses” and the greatest potential for making inroads into Portland cement’s grip on the market.
Barriers to change
But others believe geopolymers will be always limited to niche applications where their properties and handling characteristics can be used to advantage. (For example, E-Crete, according to Zeobond, is more durable that OPC in hot, humid and saline environments, such as the Middle East.)
For wider applications in major infrastructure projects such as dams, runways, hospitals and office towers, CSI’s Klee doesn’t see geopolymers overtaking OPC anytime soon.
Noel Morrin, manager for sustainability at construction group Skanska, agrees. “The world wants huge quantities of flexible, cheap, local material. And that product is Portland cement,” he says.
OPC comes at a low price because of the enormities of scale that have been developed over its 180-year history. And limestone is one of the most abundant materials on the planet, making it incredibly cheap and well distributed. “There is no way in our lifetime, or anybody else’s lifetime for that matter, that we will see cement replaced on any scale whatsoever,” says Morrin.
Inorganic aluminosilicates from waste streams such as fly ash and blast furnace slag could only supply 30% of the world’s cement needs, according to Duxson. And while natural aluminosilicates may be widely available in sources such as clay or kaolin, which make up the majority of the earth’s crust, switching to this source would require an overhaul of infrastructure for transporting and handling concrete.
Another significant barrier, especially in Europe, is the slow testing and validation process of new materials for construction. As Fredrik Glasser, chair in chemistry and cement expert at the University of Aberdeen, says: “If you build a house or a bridge or a dam, you want to be sure it will last 100 years. But it is tricky to prove to people that new materials will achieve this.”
Getting geopolymers into use hasn’t been so much of an issue in Australia, explains Duxson. In Australia, there are no official standards a product must meet before being deployed in building construction. Instead, manufacturers must gain acceptance from users to demonstrate and test small applications. “It is just a very proactive process of putting something into action, monitoring it,” he says, “and if it performs as it should after six to 12 months then moving to the next level,” which means larger and load-bearing applications.
Duxson adds that the process of getting products approved in the US is also less rigid.
Europe, however, has a set of highly prescriptive standards and validation procedures that manufacturers must follow before they can lay down even a simple footpath. “This can really hold back the introduction of new materials,” says Duxson. “The process is extremely long-winded and extremely expensive.”
Europe isn’t beyond their reach, he says, but the aim is to get wider acceptance in other markets first. “Once it has been shown that geopolymers work, there will be enormous pressure and opportunity in Europe,” he says.
Glasser agrees. “Making changes in the cement industry is slow and there isn’t a magic wand that can be waved”. Yet he is hopeful. In the 60-odd years he has been working in the field, he believes there has never been a more promising time for new breakthroughs. “There is a need for change, and the industry is perceiving that need,” he says.
You can return to the main Market News page, or press the Back button on your browser.