The Greening of Transport, One Mile at a Time
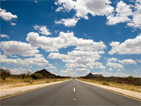
It takes about 35 billion gallons of diesel fuel to deliver goods by truck and rail each year, which generates about 350 million tons of carbon dioxide (CO2) emissions and accounts for 20 percent of all energy consumed, according to the U.S. Environmental Protection Agency’s SmartWay Transport Partnership. Truck and rail idling is responsible for about 20 percent of the CO2 emissions load.
“There are a lot of cost savings to be achieved,” says Edgar Blanco, a professor at the MIT Center for Transportation and Logistics in Cambridge, Mass. “In this economy, it makes good fiscal sense to improve fuel economy, and, there is a lot more attention being paid to energy use and carbon footprints.”
Major US companies, including retail giant Wal-Mart and SC Johnson, the manufacturer of hundreds of popular household cleaning products, are leading the trend to implement dramatic energy savings through their green logistics programs. In 2006 alone, Wal-Mart prevented 678,954 tons of carbon dioxide, 38 tons of nitrogen oxide and 1,539 tons of particulate matter from entering the atmosphere through a combination of efforts, such as the installation of Auxiliary Power Units (APUs) in diesel trucks to warm or cool the cabin on breaks.
Similarly, SC Johnson eliminated 1,882 tons of greenhouse gases, cut fuel usage by 168,000 gallons ,and saved approximately $1.6 million in 2007 through its Truckload Utilization Project, which combines multiple customer orders and products in individual trucks for maximum efficiency.
Fortunately, you don’t have to be a retail giant to achieve such dramatic savings, Blanco says. His team has helped companies of all sizes identify ways to reduce their carbon footprint through more efficient logistic strategies, and studies show there are many more companies out there looking to follow suit.
Ninety-two percent of U.S. fleet executives predict fuel prices will stay high or even rise in 2008, according to eyefortransport, a global provider of logistics and transportation information and services.
Its 2008 “Fuel Management for Fleets” report also revealed 76 percent of those surveyed rated environmental concerns as one of the most important factors in their fuel management decisions, a factor they expect to grow in significance during the next three years.
“These results were not surprising, but the consensus numbers were still higher than expected over environmental issues,” says Katharine O’Reilly, eyefortransport’s director of environmental research. “The fact that more than two-thirds of our respondents recognize the impact that environmental issues will have on their operations in the near future is encouraging.”
Xerox Takes Baby Steps
As much as 75 percent of a company’s carbon footprint can come from transportation and logistics, making it a logical target for green initiatives. As many companies have learned, there are no grand gestures when it comes to reducing fuel consumption. The most successful initiatives instead rely on small common sense programs that deliver incremental results, such as reduced idling or more direct truck routes.
These kinds of efforts are easy to implement and require little upfront investment but they can translate into big savings, notes Tony Rossi, Xerox’s manager of programs and operational support.
Rossi has sought ways to cut fuel usage of the company’s fleet of 5,000 vehicles since 2002 with remarkable results.
After surpassing its initial goal of cutting fuel consumption by 10 percent by 2005, Xerox now expects to achieve a 25 percent reduction by 2012.
“We work on it in little pieces,” he says.
His programs fall into four key areas: finding the right vehicle for each driver, buying fuel efficient vehicles, tracking mileage, and using GPS systems to send technicians to the closest client.
The “right-size” program has delivered the biggest impact. At the end of 2005, Rossi’s team looked at the vehicles each driver used to determine if it was the right size for their needs. They discovered many technicians didn’t need the storage capacity of a passenger van – which got 19 miles per gallon – could move to a fuel efficient sedan getting 25 miles per gallon. Similarly, some cargo van drivers were put in passenger vans boosting their their fuel efficiency from 15 to 19 miles per gallon. In the first year, 5 percent of drivers were moved to smaller vehicles.
“It may not sound like a lot, but it adds up,” Rossi says.
Xerox also bought 100 Toyota Prius’ for technicians who do a lot of city driving, where the fuel economy is maximized to 45 miles per gallon. It’s also investing in e85 compliant vehicles that can use the alternative fuel with a limited infrastructure. “We don’t expect a lot of benefit right away on those, but when ethanol becomes more widely available we want to have the vehicles in place to take advantage of it,” Rossi says.
With the fleet upgraded, Rossi’s team turned to mileage. It began auditing technicians’ mileage reports in 2007, which led to drivers being more aware of where they were driving and the mileage numbers they turned in.
With a baseline established, Xerox plans to implement a global positioning system in 2008 that will pair call locations with the nearest technicians. “If we know where our people are we can make smarter decisions,” Rossi says. “That will have a huge impact on our mileage.”
None of the changes made to the Xerox fleet have been radical, Rossi says.
“There are no breakthroughs in vehicle design,” he points out, “so we have to identify small ways to improve our fuel economy.”
Staples Slows Down
To help reduce its absolute CO2 emissions seven percent below 2001 levels, Staples has turned toward juggling the schedules of its drivers and reducing driving speeds.
Switching half of its truck drivers from five eight-hour days to four 10-hour days allows drivers to deliver more freight in a day. The trucks go out “two hours fuller” and deliver more while covering fewer miles with fewer trucks on the road. “It’s a successful program that doesn’t cost a thing,” says Mike Payette, fleet equipment manager for Staples.
Staples implemented a central computer system that allows Payette to limit the top speed of its fleet to 60 miles per hour. That yielded a 15 percent reduction in fuel consumption – the annual equivalent of 40,000 gallons of diesel and roughly 6,000 tons of carbon emission.
Since the drivers have to fill up less often, the new policy hasn’t added any time to their work delivery day.
“We are doing nothing more than any other fleet could do,” Payette points out. “You just need to stop and think about what you can change to make a difference.”
Bison Drivers Stay Warm
Bison Transportation, a rapidly growing truckload carrier headquartered in Winnipeg, Manitoba, constantly focuses on logistics and fuel economy, both to improve its environmental impact and to cut costs for itself and its clients, according to Jeff Pries, Bison’s vice president of sales and marketing.
“Our goal is to reduce our greenhouse gas emissions, and we are doing that through a combination of things,” Pries says.
Much of the company’s success has come from small changes or additions to the fleet and the way it is managed. Its fleet consists of 550 power units and 1,100 53-foot trailers, including air-ride and logistics vans, heated trailers and regular dry vans.
Following in the footsteps of Wal-mart, one of Bison’s most innovative solutions was the installation of in-cab auxiliary power units (APU) in all of its trucks. A previously conducted pilot program showed the heaters would have a payback period of two years on fuel savings alone, not including savings on engine life and maintenance costs. The APUs enable the drivers, who are typically on the road for days at a time, to heat the sleeping compartments and power small appliances without running the truck engine.
“The APUs use one-tenth the power that the engines require and have reduced our overall greenhouse gas emissions by 5 percent,” Pries says.
The units also keep the truck batteries charged throughout the night, which prevents freeze-ups in the cold Canada winters.
Bison saw an even bigger impact on fuel economy from launching several long combination vehicles, dubbed “Turnpikes.” These vehicles use a single cab to haul two 53-foot trailers, which are currently allowed on four-lane highways in Western Canada and some U.S. highways.
“We spent a fair bit of money developing the infrastructure to support the use of Turnpikes,” Pries admits, noting that terminals on the outskirts of town had to be established so the trucks could pull in and disconnect the two trailers before driving into the city.
The company also lobbied the governments of Manitoba, Saskatchewan, and Alberta to develop the infrastructure to support long combination trucks, including efforts to complete four-lane road widening projects.
“In some cases, we do things that have an up-front cost,” Pries says, “but they deliver savings and reduce emissions down the line. And for us, that’s the way to go.”
The effort took several years but using its 600 Turnpikes cut the company’s greenhouse gas emissions by 38 percent.
“From a fuel economy standpoint, it’s like pulling two trucks for the price of one,” Pries says, adding that the fuel economy of the combination trucks is slightly lower than the conventional trucks. “We’ve seen a huge savings in fuel consumption.”
Along with these major retrofits, the company implemented a custom training program for drivers, called Tatonka. The program identifies and shows the value of various methods of cutting fuel consumption, such as from gradual acceleration and reduced idling.
“A lot rests on the quality of the training,” Pries says. “Our drivers are professionals who want to continue improving. Our training centers aren’t set up to teach people to drive trucks. They are designed to enhance skills to create better drivers.”
To add incentive, Bison also splits the savings from reducing fuel consumption 50/50 with the drivers. “We’d rather pay that money to our drivers than send it up our smokestacks,” he says.
Getting Started
Logistics programs are easy to implement generate tangible results but must be approached with care.
“As a company, you need a strategy,” Blanco says. “Often, these programs are not done judiciously. They are launched out of fear, and that’s a mistake.”
He advises his clients to begin measuring and defining their fuel usage and goals. “There is a strong correlation between emissions and fuel consumption,” Blanco says. “A lot of carbon reduction programs result in a significant savings on oil.”
Define a baseline by identifying the amount spent on fuel, number of miles driven, or current fuel economy status before choosing a metric for measurement. For example, Xerox uses gallons of fuel used per month as its primary metric.
“It’s a simple measurement that is easy to understand,” Rossi says, “and whether we reduce miles driven, improve fuel efficiency, or reduce the number of drivers on the road, it all filters back into that single metric.”
Blanco also encourages companies to define their view of greenhouse gas emissions before setting goals for reductions and determining where to start and stop.
He notes that the EPA SmartWay program is a good resource to help establish those goals. Once you have a strategy and defined goal, start with low hanging fruit, such as monitoring tire pressure, tracking mileage, and identifying the shortest routes for drivers, then move into larger programs that require some investment.
“There is no one answer to everything,” Payette advises. “Do a lot of little things, and don’t be afraid to try something new. There are so many small opportunities, and together they all add up.”
Sarah Fister Gale is a freelance journalist based in Chicago.
You can return to the main Market News page, or press the Back button on your browser.