RISORCE raises €12.5 million for a sustainable tyre recycling plant in Belgium
This local solution is part of an industry effort to improve tyre recycling, circularity, emissions, and materials.
Belgian startup RISORCE (Renewable, Innovative Solutions towards Recycling & Circular Economy) recently raised €12.5 million investment to build a new end-of-life recycling plant in the province of Liège.
And it’s all part of an effort to make car tyres more sustainable by increasing their circularity and recyclability.
Founded in 2022, RISORCE will deploy a pyrolysis process that mainly produces oil as a byproduct from the tyres, which will be sold as a raw material to European petrochemical companies. The factory will also extract carbon black and gas, which will also be used in industrial processes or for the plant’s operating needs.
The treatment will drastically reduce the carbon emissions of used tyre materials.
Bernard van den Wouwer, Founder & CEO of RISORCE shared:
“RISORCE meets a need for local solutions in Belgium for processing tyre waste, while at the same time being firmly committed to a circular economy approach.
We are offering a locally-based solution that is both technologically and environmentally robust. A real innovation”.
The RISORCE plant will use a pyrolysis process to treat end-of-life tyres. While the methodology is not necessarily new, the application to the recycling of tyre granulates is in its infancy.
The funding is raised from a group of investors that includes GREEN.er (Recytyre), Noshaq, Wallonie Entreprendre and others.
With plans to accommodate six waste tyre processing units on the site, the project will process 18,000 tons of tyre granules annually, equivalent to 2,400,000 tyres per year.
Chris Lorquet, CEO of Recytyre, shared:
“The traditional rubber recycling industry is at a turning point. It needs to reinvent itself. The future of material circularity lies in the chemical processing of tyre components.
The RISORCE pyrolysis project is a fine example of this. I am also very pleased that this initiative is based in Wallonia. The GREEN.er fund was created to support the development of such industries at a local level.
Recovering carbon black
RISORCE has good company in Europe. In July this year, the Norwegian End-of-Life-Tyres (ELT) recycling company Wastefront received a boost to its £100 million Sunderland plant project as it entered a strategic partnership with Dutch energy company VTTI. The deal saw Wastefront receive up to $43 million in investment.
Wastefront uses pyrolytic reactors that utilize thermal depolymerization known as ‘pyrolysis’ to break down a tyre’s materials at elevated temperatures thus producing recovered carbon black (rCB). The South Tyneside plant will produce rCB from a supply of 20% of the UK’s yearly total of ELTs.
By integrating Wastefront’s rCB into new tyres, the emissions for each tyre subsequently produced will be reduced by 80%.
The need for sustainable materials is critical
Car manufacturers have been on a mission for many years to make car tyres greener in terms of materials and the impact of their use.
In 2020, UK independent emissions testing firm Emissions Analytics published a research paper claiming that tyre particulate wear emissions were 1,000 times worse than exhaust emissions. It generated a huge amount of attention, with the story translated into over 40 languages worldwide.
During driving, the rubber from car tyres wears down and flakes off into tiny airborne or roadside particles. These tyre emissions can cause damage to people’s health, air quality, soil, and water. They occur due to tyre ingredients, driving behavior, and road conditions.
It gets worse. Since their original work, the researchers have doubled down on their efforts to understand the extent of the problem. They then found that tyre wear emissions in normal driving are actually 1,850 times greater than tailpipe particulate mass emissions, almost double the previous figure for aggressive driving.
Emissions Analytics is also part of a study with the University of Portsmouth to determine the concentrations of additives in UK aquatic environments and the varying toxicity of car tyre particles from different tyre manufacturers.
Fortunately, change is coming.
In the future tyres will be made fully from sustainable materials
German tyre maker Continental plans to have all its tyres made from sustainable materials by 2050 and is working on tyres made from renewable, recycled, and traceable materials.
Materials include renewable bio-materials such as natural rubber from dandelions, silicate from rice husk, ash, and vegetable oils and resins, reducing the need for crude oil, traditionally found in tyres. Tyres will also include recycled materials materials, including reclaimed steel, recovered carbon black, and polyester yarn.
Ebikes show another way forward for circularity
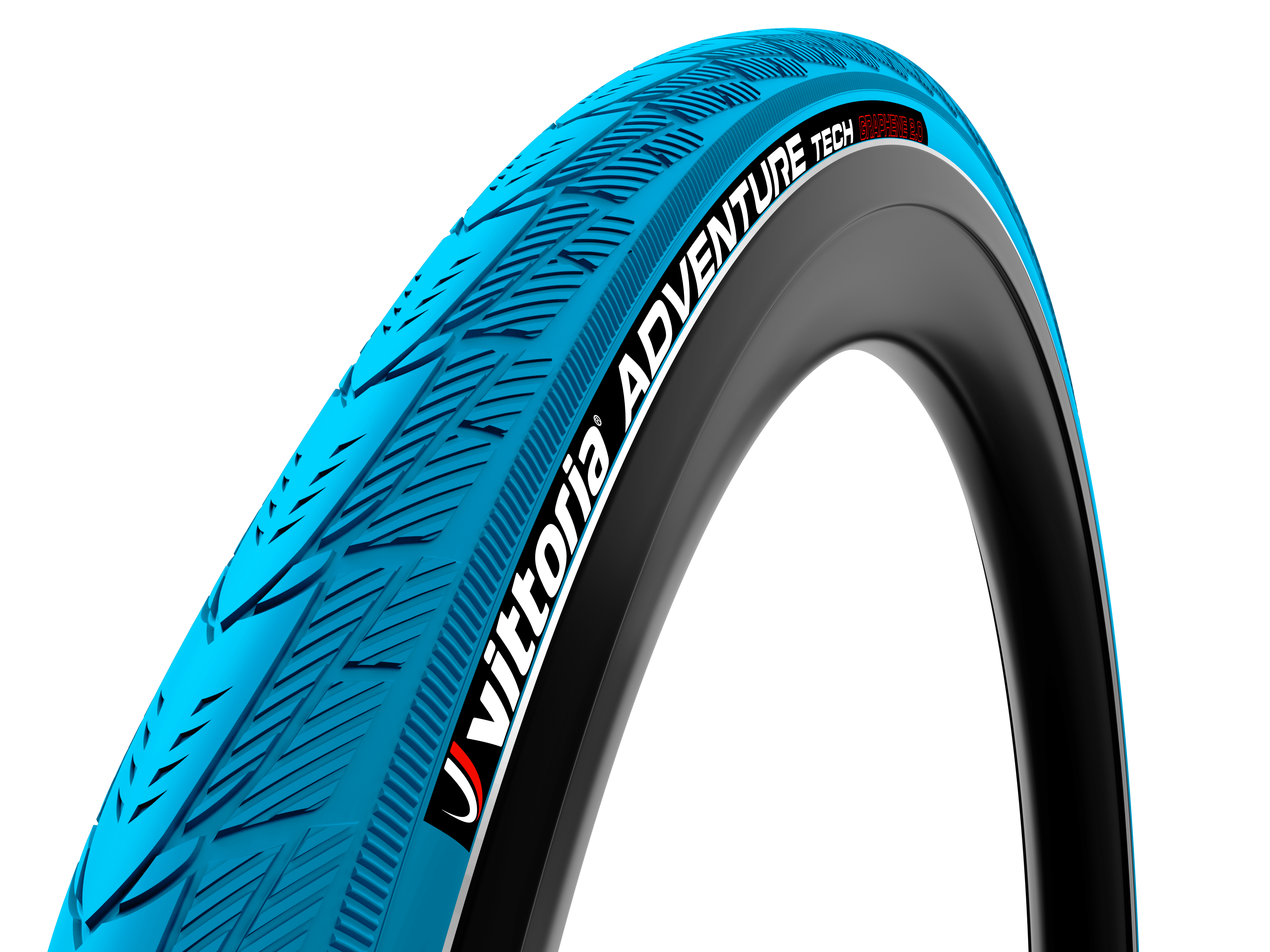
In 2021 Swapfiets became the first company to subscribe to the Vittoria2GOservice – renting tires instead of buying them. Image via Swapfiets. Photo: Uncredited.
There are also numerous circular design attempts to reduce tyre waste when it comes to ebike tyres. For example, in the Netherlands, Swapfiets has subscribed to the Vittoria2GOservice — renting tyres instead of buying them — in a key step towards achieving their goal of creating 100% circular bikes.
In the” pay for use” business model, the manufacturer handles the value of a product throughout its lifecycle. The model provides an incentive to design products optimized for durability, ease of maintenance, and repair.
Image: Acton Crawford
You can return to the main Market News page, or press the Back button on your browser.