Reusing non-chlorinated wastes saves millions
Michigan, USA - Six Gulf Coast Dow Chemical Company manufacturing facilities recently participated in a study that focused on finding ways to reuse non-chlorinated wastes. The study produced direct financial and environmental benefits for Dow, reducing waste and energy usage while improving productivity and profitability, with opportunities for $15 million in annual cost savings with little or no capital investment.
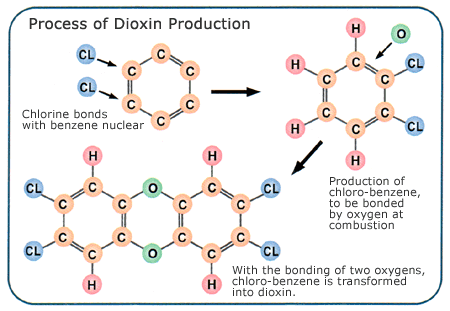
The objective of the project was to identify opportunities for waste reuse and for achieving greater synergy within Dow by crossing the boundaries between businesses, sites, and plants. The project team for the first phase of this work focused on synergy opportunities that do not require a significant capital investment.
Benefits identified during the study were wide-ranging:
In this portion of the project, participants sought ways to reuse non-chlorinated wastes and to gain experience in using the US Business Council for Sustainable Development’s By-Product Synergy (BPS) process. This was the first phase of a long-term, two-phase project. The second phase will identify synergy opportunities among other companies and industries.
Methodology
The underlying concept of BPS is that everything in the Earth’s natural ecosystem is used by some member of that system, so theoretically nothing is wasted. The BPS philosophy is to enhance the emergence of a diversified industrial ecosystem that relies on cooperation among the actors involved. In other words, industrial plants use each other’s waste material and energy as resources to minimize the amount of virgin material and energy they consume as well as the waste and emissions they produce.
BPS brings neighboring industrial companies and organizations together to exchange basic information about their processes in order to identify potential synergies. The synergies can result in added revenues, new business opportunities, cost savings, and environmental and regulatory benefits to the industrial group as well as to the group’s geographic region. The BPS methodology involves establishing a forum where engineers and experts in various processes explore reuse opportunities, collect information, and facilitate interactions among individuals, business units, and companies to identify the possibilities for reusing by-products.
In this study, the BPS methodology was combined with Dow’s Six Sigma approach to decision-making. Six Sigma is a method that is intended to virtually eliminate the defects in a process. Dow’s approach employs a series of steps described as: Define, Measure, Analyze, Improve, and Control.
Results and Projects Identified
Projects identified during the first phase of the survey were divided into six categories:
Dow is currently partnering with the U.S. Business Council for Sustainable Development to determine ways to implement the second phase of the project, which will involve identifying opportunities for synergy among various diverse companies and industries.
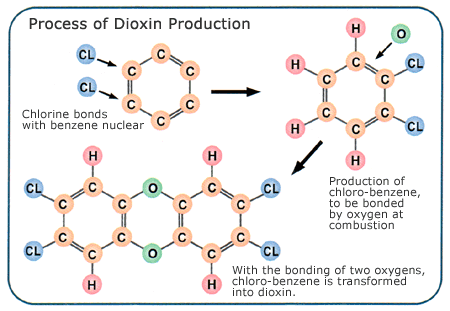
The objective of the project was to identify opportunities for waste reuse and for achieving greater synergy within Dow by crossing the boundaries between businesses, sites, and plants. The project team for the first phase of this work focused on synergy opportunities that do not require a significant capital investment.
Benefits identified during the study were wide-ranging:
- Potential annual cost savings of US$ 15 million;
- Opportunities to reduce fuel use by 900,000 MMBtu per year;
- Ways to decrease waste material production as much as 155 million pounds per year and turn the waste into useful products;
- Opportunities to reduce CO2 emissions by 108 million pounds per year.
In this portion of the project, participants sought ways to reuse non-chlorinated wastes and to gain experience in using the US Business Council for Sustainable Development’s By-Product Synergy (BPS) process. This was the first phase of a long-term, two-phase project. The second phase will identify synergy opportunities among other companies and industries.
Methodology
The underlying concept of BPS is that everything in the Earth’s natural ecosystem is used by some member of that system, so theoretically nothing is wasted. The BPS philosophy is to enhance the emergence of a diversified industrial ecosystem that relies on cooperation among the actors involved. In other words, industrial plants use each other’s waste material and energy as resources to minimize the amount of virgin material and energy they consume as well as the waste and emissions they produce.
BPS brings neighboring industrial companies and organizations together to exchange basic information about their processes in order to identify potential synergies. The synergies can result in added revenues, new business opportunities, cost savings, and environmental and regulatory benefits to the industrial group as well as to the group’s geographic region. The BPS methodology involves establishing a forum where engineers and experts in various processes explore reuse opportunities, collect information, and facilitate interactions among individuals, business units, and companies to identify the possibilities for reusing by-products.
In this study, the BPS methodology was combined with Dow’s Six Sigma approach to decision-making. Six Sigma is a method that is intended to virtually eliminate the defects in a process. Dow’s approach employs a series of steps described as: Define, Measure, Analyze, Improve, and Control.
Results and Projects Identified
Projects identified during the first phase of the survey were divided into six categories:
- Recover hydrocarbons and spent solvents
Several hydrocarbon and spent solvent streams were identified. Fifteen projects were identified in this category, and seven were recommended for implementation, each with significant benefits depending on the technology used. For example, if advanced separation technology could effectively separate ethyl acrylate and acrylic acid for reuse, incineration cost savings in combination with new revenue from recovered products could amount to as much as $3 million per year. If new uses of the by-product as-is, or with little processing, could be identified, savings could also be close to $3 million per year with little or no need for a major capital expense. - Reuse sodium hydroxide by-product
Several million pounds per year of low-concentration (1%–5%) sodium hydroxide (NaOH) solution are generated in the plants that were studied. Currently, much of this material is neutralized with acid and then discarded. One successful project to convert a weak alkalinity by-product stream to magnesium hydroxide could yield estimated cost savings between $640,000 and $1.6 million. - Reuse Methocel waste
Highly concentrated Methocel waste is currently incinerated. Synergy opportunities identified include recovery of the crude cellulose ether, and making use of the physical and chemical properties that are attributes of the by-product to fulfill existing performance chemical needs and to create new applications. - Reuse ortho-toluenediamine
Ortho-toluenediamine (OTDA) is a relatively pure compound with no end-use customer. It is currently incinerated at a cost of hundreds of thousands of dollars per year. Synergy opportunities identified include (1) use the OTDA to manufacture polyols (polyols are alcohols having many hydroxyl radicals, and they include polyethers, glycols, polyesters, and castor oil; polyol, also known as polyhydric alcohol, is used as a reactant.); (2) sell it as raw material for use in manufacturing antioxidants, corrosion inhibitors, rubber chemicals, and dyes; and (3) make use of the physical and chemical properties that are attributes of the by-product to meet current performance chemical needs and to create new applications. - Reuse by-product hydrogen
The BPS project team discovered that some plants produce by-product hydrogen of various qualities, including “ultra-pure.” They also discovered that other industrial plants buy pure hydrogen to use as a feedstock. The opportunity for synergy is to link plants that produce hydrogen as a by-product with those that can use it as feedstock.
Dow is currently partnering with the U.S. Business Council for Sustainable Development to determine ways to implement the second phase of the project, which will involve identifying opportunities for synergy among various diverse companies and industries.
You can return to the main Market News page, or press the Back button on your browser.