Does Recycling Plastic Cost More Than Making It?
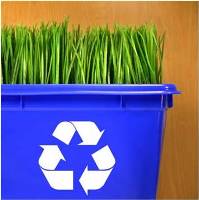
Setting aside environmental concerns, the economic success or failure of plastics recycling relies on two variables: the cost of the raw materials used to make virgin plastic, petroleum and natural gas, and the cost of recycling versus the cost of disposal, which fluctuates based on a city’s proximity to recycling centers and the price to dump in local landfills. A University of California, Berkeley study estimated that areas like Los Angeles and San Francisco could gain an economic benefit of $200 a ton for recycling instead of dumping. Nonetheless, the cost of recycling a bottle versus making a new one simply varies, depending where the bottle is and what the capricious price of oil happens to be.
Each year, 29 billion plastic water bottles are produced for use in the United States, according to the Earth Policy Institute, an environmental organization in Washington, D.C. Manufacturing them requires the equivalent of 17 million barrels of crude oil, so rising oil and natural gas prices have only exacerbated the high price of virgin plastic. “Plastics News,” a trade magazine, lists the recent price of PET virgin bottle resin pellets between 83 and 85 cents a pound, compared to only 58 to 66 cents a pound for PET recycled pellets.
Yet escalating plastic prices have done little to curb demand. The amount of PET plastic on U.S. shelves has more than doubled in the last decade, according to the National Association for PET Container Resources (NAPCOR). The increase is a result of the surging demand for bottled water. In 2005, seven and a half billion gallons of water flooded U.S. shelves – roughly equivalent to the average amount of water that flows over Niagara Falls in three hours. That’s 21 times more bottled water than the amount available on shelves in 1976, according to U.S. government data.
All that extra plastic, and the petroleum used to make it, is expensive. NAPCOR estimates that 5.5 billion pounds of PET bottles and jars passed over U.S. shelves in 2006. Making this many PET bottles and jars today from virgin plastic would cost $4.5 billion just for the raw materials, without considering the cost of operating bottle production plants.
Prior to its reincarnation as industrial carpet or sleeping bag stuffing, a plastic bottle in the recycle bin has a long journey ahead of it. First it goes to a collection facility to be inspected for contaminants like rock or glass. Then it is washed and chopped into flakes. The flakes are dried and melted into plastic lava, which is filtered for impurities and formed into strands. Finally, the strands are cooled in water and chopped into pellets that can go to market.
Landfills, however, are the final resting place for most bottles. Ostensibly this is the cheaper option. But landfill tipping fees, the dumping tariffs levied to offset the cost of creating, maintaining and closing a landfill, can be quite expensive compared to recycling. This is especially true in densely populated areas like the East Coast or areas like Florida with shallow water tables. In fact, fees can run from $10 a ton to over $100, according to Jerry Powell, editor of the trade publication “Plastics Recycling Update.” Additionally, dumping wastes a valuable commodity: In 2005, about half a billion dollars worth of PET bottles went to landfills, according to the Container Recycling Institute, a non-profit organization.
Rising plastic prices have forced some companies that bottle their product, like Coca-Cola, to think twice about using expensive virgin plastic resin. Now they are working to make more lightweight bottles that contain more recycled resin, Powell explained. Bottles made with thinner plastic use 30 percent less resin and rely on the water or liquid inside to maintain their shape. Using less resin per bottle could translate to a savings on raw materials of about $1.5 billion a year for the bottling industry. Powell thinks it’s a positive step for business and the environment. “That’s what we need,” he remarked. “Less plastic. Not just recycling.”
This answer is provided by Scienceline, a project of New York University’s Science, Health and Environmental Reporting Program.
By Christopher Intagliata, Scienceline
You can return to the main Market News page, or press the Back button on your browser.