Bhopal Redux - The Same Risks Remain Elsewhere
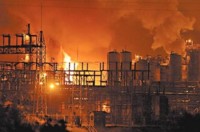
Ltd. were convicted of “death by negligence” and sentenced to
two-year jail terms for their roles in the release of a chemical
that killed thousands in Bhopal, India, more than 25 years ago.
Regulators in the United States, meanwhile,
are still grappling with how to handle the same chemical – methyl
isocyante, or MIC – at a pesticide plant in West Virginia.
The Bayer CropScience plant in Institute, W.Va., is the last
facility in the U.S. to store large quantities of MIC, used to
manufacture carbamate pesticides and, to a lesser degree, rubber
and adhesives.
Congress last year ordered the target=”_blank” title=”U.S. Chemical Safety Board”>U.S. Chemical
Safety Board to study the use of MIC after a 2008 explosion at
the Bayer CropScience plant threatened to release 14,000 pounds of
the chemical. The blast, which killed two workers, occurred within
80 feet of the MIC storage tank.
“During the explosion, metal projectiles weighing up to a
hundred pounds flew in all directions,” Chemical Safety Board
Chairman John Bresland said in congressional testimony last year.
If the tank had been pierced, “There might have been a catastrophic
impact on workers, responders, and the public,” he said.
After the accident, Bayer CropScience promised to reduce its MIC
storage by 80 percent and move it underground. “We believe our
manufacturing process coupled with the change we’re implementing
will provide the highest levels of safety for our work force and
the community,” said company spokesman Jack Boyne.
But there are skeptics.
“BP believed their processes were safe, too,” said Maya Nye, one
of Institute’s 10,000 residents and a spokeswoman for People
Concerned About MIC. “That doesn’t make the seafood farmers of the
Gulf Coast feel much better. I don’t think anyone with any sort of
common sense can feel secure by that company line anymore,
especially coming from a company that nearly caused another Bhopal
to happen in our community.”
Rick Hind, legislative director for Greenpeace in Washington,
said the company’s plan to cut its inventory did not go far enough.
“They’re still going to have the largest [MIC stockpile] in the
country, more than 25 years after Bhopal and decades after
everybody else has gotten out of this,” Hind said.
The Chemical Safety Board has been soliciting public comments to
prepare for a National Academy of Sciences study of MIC and perhaps
other highly toxic chemicals. John Vorderbrueggen, an
investigations supervisor with the board, said he hopes the scope
of the study will be defined and a contract with the academy signed
within the next eight weeks.
Greenpeace’s Hind questions the need to study MIC, whose hazards
are well documented, and worries that it will allow Bayer to keep
using the chemical indefinitely.
The study, however, could lead to broader safety reforms that go
beyond MIC.
“Although [the 2008] incident is specific to one type of
chemical, the CSB’s goal is to get the message out to industry of
the importance of safely managing all toxic chemicals,”
Vorderbrueggen said. “The ultimate goal is to continue to improve
the operating safety of any toxic chemical operation.”
Earlier this year, Bayer CropScience, a division of the German
conglomerate target=”_blank” title=”Bayer AG”>Bayer AG, was fined $143,000
by the Occupational Safety and Health Administration for the 2008
explosion.
The same West Virginia plant has had a series of owners and a
variety of other accidents over the years. Rhone-Poulenc, the
French company that owned the plant before Bayer CropScience,
agreed to pay $700,000 in fines in connection with an August 1994
explosion that killed one worker. Two years later, Rhone-Poulenc
paid $450,000 in fines following a chemical release.
In August 1985, only eight months after the Bhopal disaster, a
cloud containing acutely toxic aldicarb oxide and four other
chemicals leaked from the West Virginia plant, then owned by Union
Carbide. The accident sent 135 people to the hospital.
According to a 1993 report commissioned by the Environmental
Protection Agency, the release went undetected by workers because a
high-temperature alarm was out of service, a level indicator in the
tank was broken, a newly installed gas detection system had not
been set to test for aldicarb oxide, and a water-spray system that
was supposed to keep the gas from going offsite wasn’t up to the
task.