Bridgestone Claims Polymeric Core-Shell Nanoparticles Superior to Carbon Black Fillers in Tire and Rubber Applications
Bridgestone Americas (Akron, OH) reveals new polymeric interphase nanoparticles that represent a potential threat to the 8 million ton per year carbon black market. In U.S. Patent Application 20100004398, Bridgestone details nanoparticles for use as filler in rubber and plastic compounds. The resulting rubber compounds with added polymeric interphase nanoparticles exhibit superior strength, hardness, improved tensile and tear strength as well as barrier qualities compared to rubber and plastic compounds filled with carbon black fillers.
To see how Klean Industries is changing material science within the tire and rubber related formulation industry with environmentally friendly, cost effective nano technologies please click here.
FIG. 10 is an atomic force micrograph of Bridgestone Americas’ new polymeric interphase nanoparticles. A key use for polymeric nanoparticle rubber compounds is tire rubber formulations to make tire treads and side walls. The inventive interphase polymeric nanoparticles “exhibit unexpectedly better storage modulus and well as loss modulus than the control with carbon black particles.”
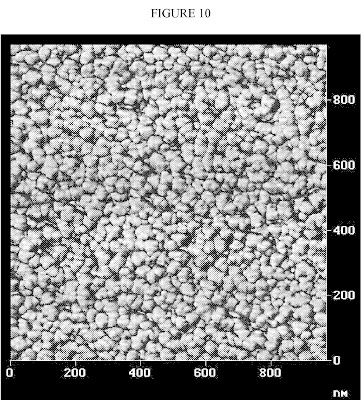
Bridgestone Americas’ nanoparticles may be of a core/shell configuration with an interphase region connecting the core and the shell. The mean average diameter of the polymer nanoparticles may be less than about 250 nanometers (nm). The interphase region is from about 1 nm to about 100 nm.
The size, composition, and/or configuration of the interphase region may be varied to achieve desired physical and/or chemical properties of the resulting polymeric nanoparticles, and of the compositions into which the nanoparticles are compounded, according to inventors Xiaorong Wang, Georg Bohm, Sandra Warren, Xiao-Dong Pan and James E. Hall in U.S. Patent Application 20100004398,
Bridgestone’s polymeric nanoparticles with at least one interphase region exhibit “unexpected super-elasticity. Its tensile at break, and especially its elongation at break, far exceeded those for the control compound,” which contained no polymeric nanoparticles and instead contained 50 phr of conventional reinforcing carbon black.
A core/shell configuration refers generally to a polymeric nanoparticle with at least two defined regions, in which one region (called herein the core) is substantially surrounded by another region (called herein the shell). The core region and the shell region may each have one or more layers.
FIG. 1b is an illustration of several spherical-shaped nanoparticles interacting and attached to each other at their interphase regions.
In particular, FIG. 1b depicts an embodiment in the which the nanoparticles are comprised of a styrene/divinylbenzene core, a relatively narrow polystyrene interphase region, and a butadiene/styrene shell in the form of brushes. Such nanoparticles lead to unexpectedly improved physical properties when the interacting nanoparticles are compounded into a rubber composition. The nanoparticles may interact or connect with each other at their shell regions. FIG. 1b also depicts some interaction between nanoparticles at their shell regions.
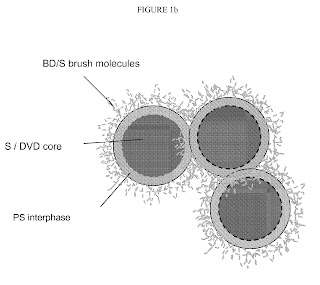
Polymeric nanoparticles have attracted increased attention over the past several years in a variety of fields including catalysis, combinatorial chemistry, protein supports, magnets, and photonic crystals. Similarly, vinyl aromatic (e.g., polystyrene) microparticles have been prepared for uses as a reference standard in the calibration of various instruments, in medical research, and in medical diagnostic tests.
Nanoparticles can be discrete particles uniformly dispersed throughout a host composition. Nanoparticles may be monodisperse in size and uniform in shape. However, controlling the size of nanoparticles during polymerization, the surface characteristics, and/or the internal composition of such nanoparticles can be difficult. Moreover, achieving better control over the surface composition and/or the internal composition of polymeric nanoparticles also is desirable.
Rubbers may be modified by the addition of various polymer compositions. Such polymeric additives often improve the physical properties of rubber compositions. Specifically, moldability and tenacity are often improved through such modifications.
Development of nanoparticles having, in part, a poly(conjugated diene) surface layer that would be compatible with a wide variety of rubbers may be desirable because discrete particles could likely disperse evenly throughout the rubber to provide a uniform rubber composition.
The size, composition, and/or configuration of the interphase region may be varied to achieve desired physical and/or chemical properties of the resulting polymeric nanoparticles, and of the compositions into which the nanoparticles are compounded.
A method for forming polymeric nanoparticles may include self-assembly of a plurality of polymer chains into one or more nanoparticles. A rubber composition may be formed, wherein the above-described nanoparticles are combined with at least one rubber to form a modified rubber composition possessing at least one of improved tensile and tear strength.
“Rubber” refers to rubber compounds, including natural rubber, and synthetic elastomers, including styrene-butadiene rubber and ethylene propylene rubber.
Nanoparticles are spherical or substantially .spherical, as shown in FIG. 1b. In another embodiment, the nanoparticles have a string shape, as shown in FIG. 2. In a further embodiment, the nanoparticles have a flower shape, as shown in FIG. 3. In another embodiment, the nanoparticles have an ellipsoid shape.
FIG. 2 is a nanoparticle in string shape. FIG. 3 is a nanoparticle in flower shape.
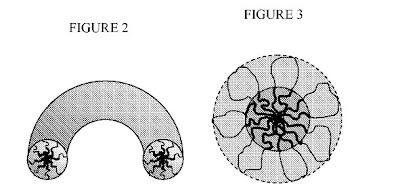
FIG. 7 is an atomic force micrograph of nanoparticles without an interphase region made by Bridgestone.
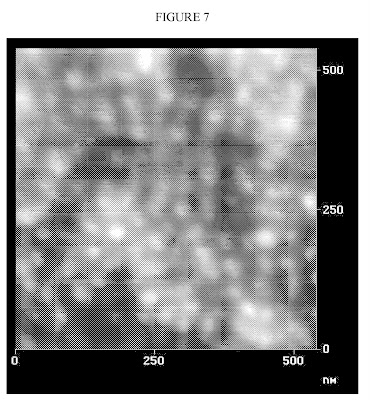
FIG. 8 is another atomic force micrograph of the nanoparticles without an interphase region made by Bridgestone.
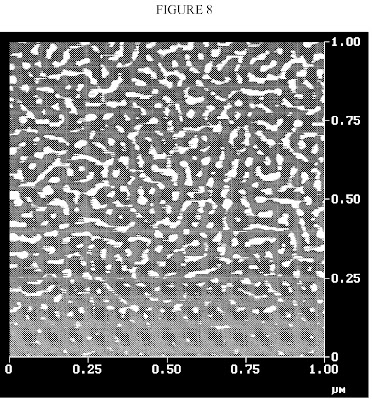
FIG. 9 is an atomic force micrograph of the polymeric interphase nanoparticles made by Bridgestone.
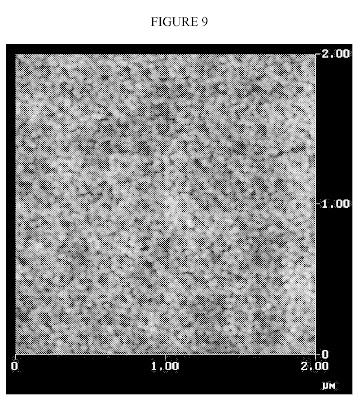
FIG. 11 is a further atomic force micrograph of the polymeric interphase nanoparticles made by Bridgestone.
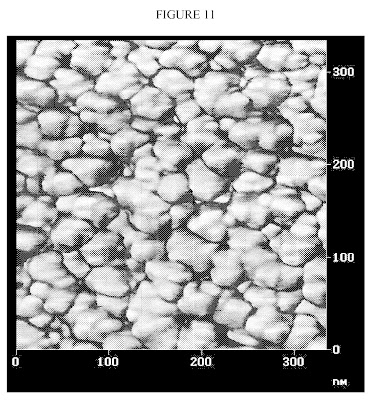
FIG. 13 is an atomic force micrograph showing the dispersion of the carbon black particles in the rubber compound. FIG. 13 is an electron micrograph showing the dispersion of the carbon black particles in the rubber compound. FIG. 14 is an electron micrograph showing the dispersion of the interphase nanoparticles from this Example in the rubber compound. A comparison of FIG. 13 to FIG. 14 reveals that the interphase nanoparticles were more uniformly dispersed in the rubber compound than the carbon black particles.
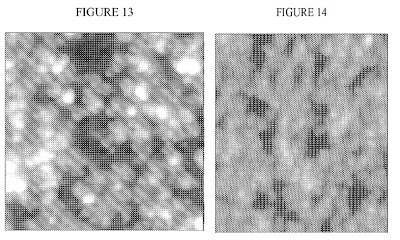
To see how Klean Industries is changing material science within the tire and rubber related formulation industry with environmentally friendly, cost effective nano technologies please click here.
FIG. 10 is an atomic force micrograph of Bridgestone Americas’ new polymeric interphase nanoparticles. A key use for polymeric nanoparticle rubber compounds is tire rubber formulations to make tire treads and side walls. The inventive interphase polymeric nanoparticles “exhibit unexpectedly better storage modulus and well as loss modulus than the control with carbon black particles.”
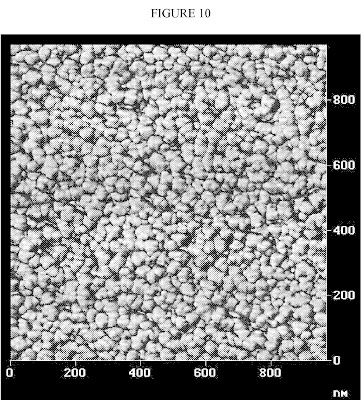
Bridgestone Americas’ nanoparticles may be of a core/shell configuration with an interphase region connecting the core and the shell. The mean average diameter of the polymer nanoparticles may be less than about 250 nanometers (nm). The interphase region is from about 1 nm to about 100 nm.
The size, composition, and/or configuration of the interphase region may be varied to achieve desired physical and/or chemical properties of the resulting polymeric nanoparticles, and of the compositions into which the nanoparticles are compounded, according to inventors Xiaorong Wang, Georg Bohm, Sandra Warren, Xiao-Dong Pan and James E. Hall in U.S. Patent Application 20100004398,
Bridgestone’s polymeric nanoparticles with at least one interphase region exhibit “unexpected super-elasticity. Its tensile at break, and especially its elongation at break, far exceeded those for the control compound,” which contained no polymeric nanoparticles and instead contained 50 phr of conventional reinforcing carbon black.
A core/shell configuration refers generally to a polymeric nanoparticle with at least two defined regions, in which one region (called herein the core) is substantially surrounded by another region (called herein the shell). The core region and the shell region may each have one or more layers.
FIG. 1b is an illustration of several spherical-shaped nanoparticles interacting and attached to each other at their interphase regions.
In particular, FIG. 1b depicts an embodiment in the which the nanoparticles are comprised of a styrene/divinylbenzene core, a relatively narrow polystyrene interphase region, and a butadiene/styrene shell in the form of brushes. Such nanoparticles lead to unexpectedly improved physical properties when the interacting nanoparticles are compounded into a rubber composition. The nanoparticles may interact or connect with each other at their shell regions. FIG. 1b also depicts some interaction between nanoparticles at their shell regions.
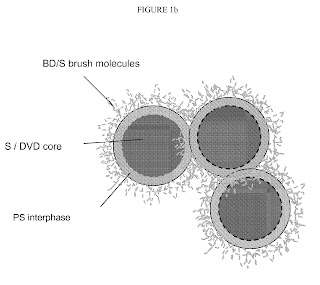
Polymeric nanoparticles have attracted increased attention over the past several years in a variety of fields including catalysis, combinatorial chemistry, protein supports, magnets, and photonic crystals. Similarly, vinyl aromatic (e.g., polystyrene) microparticles have been prepared for uses as a reference standard in the calibration of various instruments, in medical research, and in medical diagnostic tests.
Nanoparticles can be discrete particles uniformly dispersed throughout a host composition. Nanoparticles may be monodisperse in size and uniform in shape. However, controlling the size of nanoparticles during polymerization, the surface characteristics, and/or the internal composition of such nanoparticles can be difficult. Moreover, achieving better control over the surface composition and/or the internal composition of polymeric nanoparticles also is desirable.
Rubbers may be modified by the addition of various polymer compositions. Such polymeric additives often improve the physical properties of rubber compositions. Specifically, moldability and tenacity are often improved through such modifications.
Development of nanoparticles having, in part, a poly(conjugated diene) surface layer that would be compatible with a wide variety of rubbers may be desirable because discrete particles could likely disperse evenly throughout the rubber to provide a uniform rubber composition.
The size, composition, and/or configuration of the interphase region may be varied to achieve desired physical and/or chemical properties of the resulting polymeric nanoparticles, and of the compositions into which the nanoparticles are compounded.
A method for forming polymeric nanoparticles may include self-assembly of a plurality of polymer chains into one or more nanoparticles. A rubber composition may be formed, wherein the above-described nanoparticles are combined with at least one rubber to form a modified rubber composition possessing at least one of improved tensile and tear strength.
“Rubber” refers to rubber compounds, including natural rubber, and synthetic elastomers, including styrene-butadiene rubber and ethylene propylene rubber.
Nanoparticles are spherical or substantially .spherical, as shown in FIG. 1b. In another embodiment, the nanoparticles have a string shape, as shown in FIG. 2. In a further embodiment, the nanoparticles have a flower shape, as shown in FIG. 3. In another embodiment, the nanoparticles have an ellipsoid shape.
FIG. 2 is a nanoparticle in string shape. FIG. 3 is a nanoparticle in flower shape.
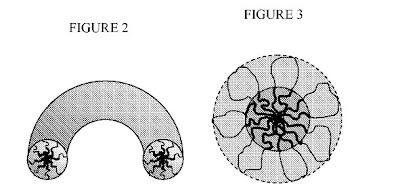
FIG. 7 is an atomic force micrograph of nanoparticles without an interphase region made by Bridgestone.
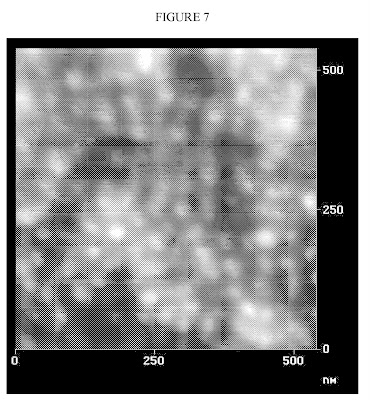
FIG. 8 is another atomic force micrograph of the nanoparticles without an interphase region made by Bridgestone.
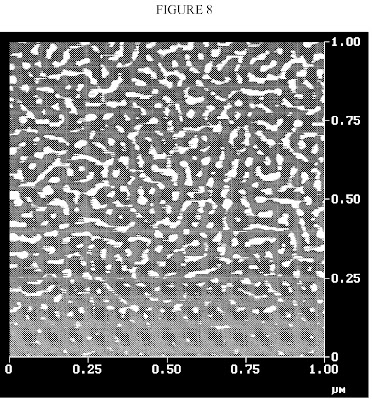
FIG. 9 is an atomic force micrograph of the polymeric interphase nanoparticles made by Bridgestone.
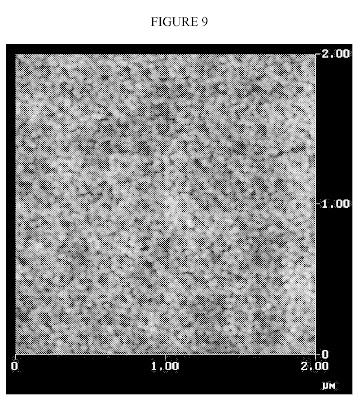
FIG. 11 is a further atomic force micrograph of the polymeric interphase nanoparticles made by Bridgestone.
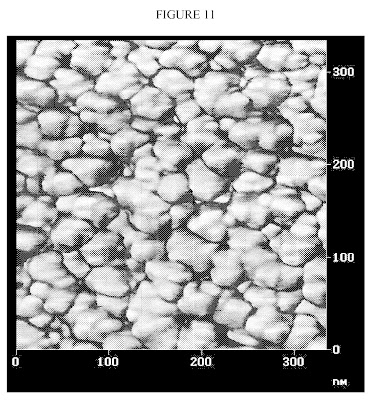
FIG. 13 is an atomic force micrograph showing the dispersion of the carbon black particles in the rubber compound. FIG. 13 is an electron micrograph showing the dispersion of the carbon black particles in the rubber compound. FIG. 14 is an electron micrograph showing the dispersion of the interphase nanoparticles from this Example in the rubber compound. A comparison of FIG. 13 to FIG. 14 reveals that the interphase nanoparticles were more uniformly dispersed in the rubber compound than the carbon black particles.
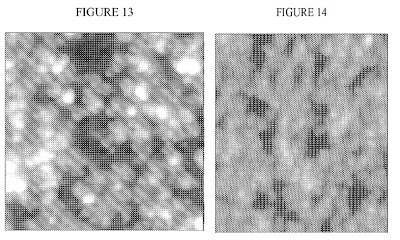
FIG. 19 depicts interphase nanoparticles dispersed in a rubber polymer matrix according Bridgestone .
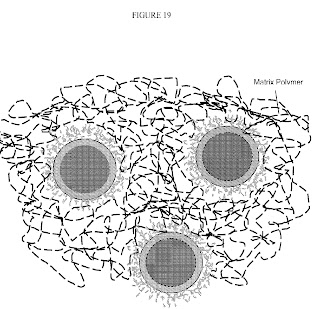
The core, shell, and interphase region of the inventive polymeric nanoparticles may be made from polymerizable monomers, which may be referred to herein as units. At least one monomer that polymerizes to form the core region may be referred to herein as a core monomer. At least one monomer that polymerizes to form the shell region may be referred to herein as a shell monomer. The core, shell, and at least one interphase region of the polymeric nanoparticles may be formed from one polymer, such as a random, a monoblock, or a multiblock polymer, or from different polymers bonded or otherwise aggregated together.
The shapes of the nanoparticles may be controlled by various methods, for instance: (1) varying the concentration of monomers during polymer formation; (2) including at least three blocks of a multiblock polymer, or at least two polymers, in the core or shell, and (3) varying the molecular weight of the polymers used to create the polymeric nanoparticles. In one embodiment, the core may include a triblock polymer represented by the formula S-B-S, in which S indicates a styrene block and B represents a butadiene block. In one such embodiment, the triblock polymer is a portion of a larger multiblock polymer. In another embodiment, the molecular weight is varied by increasing the ratio of shell monomer to core monomer, which may produce nanoparticles with an ellipsoid shape.
The crosslinking agent is a divinylbenzene mixture comprising at least two benzenes chosen from ortho-divinylbenzene, meta-divinylbenzene, para-divinylbenzene, ortho-ethylvinylbenzene, meta-ethylvinylbenzene, and para-ethylvinylbenzene.
You can return to the main Market News page, or press the Back button on your browser.